Centrifugal barrel polishing mechanical pre-polishing method for copper cavity substrate
A technology of roller polishing and substrate, applied in polishing compositions containing abrasives, grinding/polishing equipment, machine tools for surface polishing, etc., can solve the problems of affecting the quality of vacuum coating, unsatisfactory effect, low repeatability, etc.
- Summary
- Abstract
- Description
- Claims
- Application Information
AI Technical Summary
Problems solved by technology
Method used
Image
Examples
Embodiment Construction
[0039] The present invention will be described in further detail below in conjunction with the accompanying drawings.
[0040] The present invention aims to explore a set of centrifugal tumbling and polishing formula applied to the base of copper cavity, which is convenient for subsequent chemical polishing or electropolishing, so as to carry out vacuum coating. The principle diagram of centrifugal rolling and throwing is attached figure 1As shown, including the 1.3GHz ellipsoidal copper cavity substrate to be polished, the directions of rotation and revolution in centrifugal tumbling are completely opposite. Under the joint action of rotation and revolution, the centrifugal force on the abrasive is perpendicular to the cavity wall (normal direction), and the abrasive and the cavity wall move relative to each other in a tangential direction, thereby producing a polishing effect on the cavity wall. Abrasive selection, dosage, time, temperature and other factors directly deter...
PUM
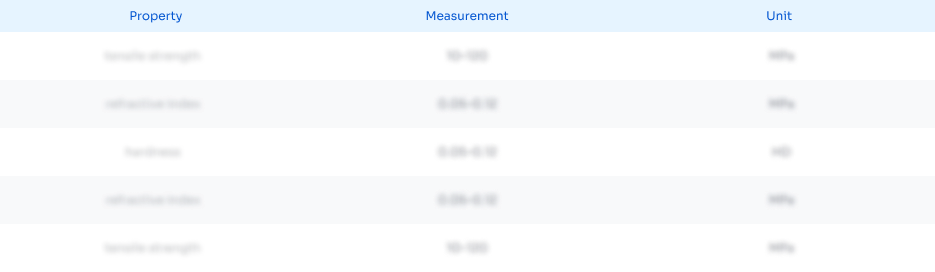
Abstract
Description
Claims
Application Information

- R&D Engineer
- R&D Manager
- IP Professional
- Industry Leading Data Capabilities
- Powerful AI technology
- Patent DNA Extraction
Browse by: Latest US Patents, China's latest patents, Technical Efficacy Thesaurus, Application Domain, Technology Topic, Popular Technical Reports.
© 2024 PatSnap. All rights reserved.Legal|Privacy policy|Modern Slavery Act Transparency Statement|Sitemap|About US| Contact US: help@patsnap.com