Composite anticorrosive pigment and preparation method and application thereof
A kind of anti-corrosion pigment and composite technology, applied in the field of anti-corrosion pigment, can solve the problems of single anti-corrosion matrix, pigment performance limitation, etc., and achieve the effect of consistent refractive index, low pore volume, and high bulk density
- Summary
- Abstract
- Description
- Claims
- Application Information
AI Technical Summary
Problems solved by technology
Method used
Image
Examples
Embodiment 1
[0030] 1) Preparation of silica with low water porosity and low oil absorption: add 500 g of dilute sulfuric acid solution with a concentration of 30% to the reaction vessel, start stirring, and slowly add sodium silicate solution (modulus 3.1-3.4, SiO 2 % (wt=10%) is about 3.1kg, and the addition time is 30 minutes. At this time, the pH is about 6, and it is stirred for 15 minutes, which is low water porosity and low oil absorption silica.
[0031] 2) Introduction of calcium phosphate and calcium ion source: add 450g supersaturated calcium hydroxide solution (calcium oxide: water ratio 1:8) to the above system, stir for 20 minutes, slowly add dilute phosphoric acid solution (concentration: 30%) about 33.3g, at this time the pH is 8-9, then add 120g of calcium chloride solid, and stir for 20 minutes.
[0032] 3) Coating and pulverization of the wax solution: in step 2, the temperature of the system is raised to 80° C., and about 250 g of oxidized polyethylene wax emulsion (wax...
Embodiment 2
[0034] 1) Preparation of silica with low water porosity and low oil absorption: add 1.2 kg of dilute sulfuric acid solution with a concentration of 20% to the reaction vessel, start stirring, and slowly add sodium silicate solution (modulus 3.1-3.4, SiO 2 % (wt=5%) is about 9.9kg, and the addition time is 50min. At this time, the pH is about 6. After stirring and standing for 1.5h, it is silica with low water porosity and low oil absorption.
[0035] 2) Introduction of calcium phosphate and calcium ion source: add 640g supersaturated calcium hydroxide solution (calcium oxide: water ratio 1:7) to the above system, stir for 30 minutes, slowly add dilute phosphoric acid solution (concentration: 30%) about 56g, at this time the pH was 8-9, and then 190g of calcium chloride solid was added and stirred for 30 minutes.
[0036] 3) Coating and pulverization of the wax solution: in step 2, the temperature of the system was raised to 90° C., and about 416 g of oxidized polyethylene wax ...
Embodiment 3
[0038]1) Preparation of silica with low water porosity and low oil absorption: add 300 g of dilute sulfuric acid solution with a concentration of 40% to the reaction vessel, start stirring, and slowly add sodium silicate solution (modulus 3.1-3.4, SiO 2 % (wt=20%) is about 1.3kg, and the addition time is 20 minutes. At this time, the pH is about 6, and it is stirred for 15 minutes, which is low water porosity and low oil absorption silica.
[0039] 2) Introduction of calcium phosphate and calcium ion source: add 410g supersaturated calcium hydroxide solution (calcium oxide: water ratio 1:9) to the above system, stir for 20 minutes, slowly add dilute phosphoric acid solution (concentration: 30%) about 23g, at this time the pH was 8-9, then 95g of calcium chloride solid was added and stirred for 20 minutes.
[0040] 3) Coating and pulverization of the wax solution: in step 2, the temperature of the system was raised to 85° C., and about 208 g of oxidized polyethylene wax emulsio...
PUM
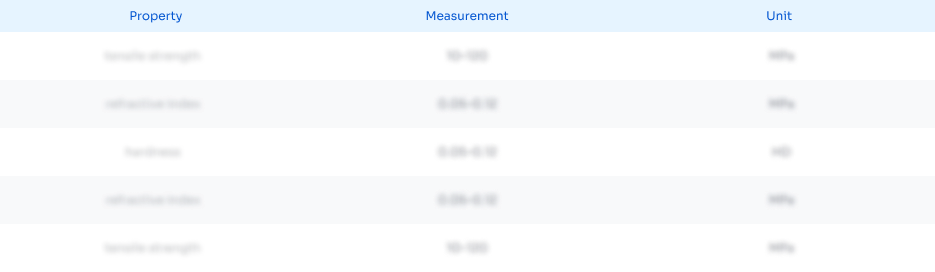
Abstract
Description
Claims
Application Information

- R&D Engineer
- R&D Manager
- IP Professional
- Industry Leading Data Capabilities
- Powerful AI technology
- Patent DNA Extraction
Browse by: Latest US Patents, China's latest patents, Technical Efficacy Thesaurus, Application Domain, Technology Topic, Popular Technical Reports.
© 2024 PatSnap. All rights reserved.Legal|Privacy policy|Modern Slavery Act Transparency Statement|Sitemap|About US| Contact US: help@patsnap.com