Blister molding method for anti-static plastic sheet
A technology of plastic sheet and process method, applied in the direction of static electricity, electrical components, flat products, etc., can solve the problems of static electricity hazard, stay, safety hazard, etc., and achieve the effect of antistatic
- Summary
- Abstract
- Description
- Claims
- Application Information
AI Technical Summary
Problems solved by technology
Method used
Image
Examples
Embodiment 1
[0043] see Figure 1-3 , a kind of antistatic plastic sheet blister forming process, the specific process steps are as follows:
[0044] S1. Preparatory work: prepare the plastic sheet, clean and dry the plastic sheet and the blow cavity of the blow mold, and attach a layer of hot-melt fiber net 4 to the upper and lower end surfaces of the plastic sheet;
[0045] S2. Anti-static treatment before blow molding: through a pair of anti-static rollers 2, the plastic sheet body 1 is driven into the blow mold, and the blow mold and a pair of anti-static rollers 2 are placed on the pair of anti-static rollers 2. A spraying box 3 is arranged between them, and the spraying box 3 is filled with a plurality of antistatic agent powders 5. Before the plastic sheet body 1 is driven into the blow mold, the upper and lower end surfaces of the plastic sheet body 1 are sprayed with antistatic agents. Static agent powder 5;
[0046] S3. Antistatic molding: in S2, after 5 is attached to the hot-...
PUM
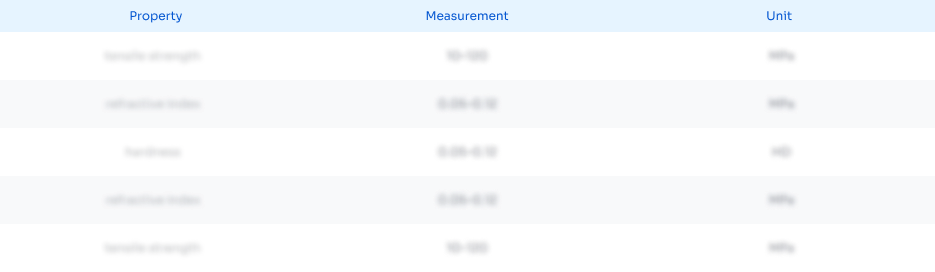
Abstract
Description
Claims
Application Information

- R&D
- Intellectual Property
- Life Sciences
- Materials
- Tech Scout
- Unparalleled Data Quality
- Higher Quality Content
- 60% Fewer Hallucinations
Browse by: Latest US Patents, China's latest patents, Technical Efficacy Thesaurus, Application Domain, Technology Topic, Popular Technical Reports.
© 2025 PatSnap. All rights reserved.Legal|Privacy policy|Modern Slavery Act Transparency Statement|Sitemap|About US| Contact US: help@patsnap.com