Catalyst and preparation method, flue gas CO removal-whitening system and method
A catalyst and flue gas technology, used in chemical instruments and methods, physical/chemical process catalysts, metal/metal oxide/metal hydroxide catalysts, etc. Problems such as poor white effect
- Summary
- Abstract
- Description
- Claims
- Application Information
AI Technical Summary
Problems solved by technology
Method used
Image
Examples
preparation example Construction
[0034] In order to solve the problem that there is still a considerable amount of CO at the end of the flue gas in the prior art, and the flue gas also contains a large amount of water vapor, and the problem of white feathers will be formed when the flue gas is directly discharged at low altitude, the first aspect of the present invention provides a catalyst preparation method, including Follow the steps below:
[0035] 1) Dissolve aluminum isopropoxide powder in deionized water, heat in a water bath to 85° C., stir mechanically for 1 h, adjust the pH value of the solution with acid, and prepare aluminum sol after stirring in a water bath.
[0036] 2) Dissolve a certain amount of organic salts of copper, manganese, iron, cerium, titanium, and zirconium in ethanol, add cationic polyacrylamide, adjust the pH value, stir in a mechanical stirrer at room temperature, and place the mixture in a hydrothermal The hydrothermal synthesis reaction is carried out in the reactor.
[0037]...
Embodiment 1
[0076] Catalyst preparation method:
[0077] 1) Dissolve 10kg of aluminum isopropoxide in 10kg of deionized water, heat in a water bath to 85°C, and stir mechanically for 1 hour. The pH value of the solution was adjusted to 3.5 with 1mol / L acetic acid, and the aluminum sol was obtained after stirring for 12 hours.
[0078] 2) Dissolve 804.67g of copper citrate, 1.3kg of manganese L-aspartate, 12.7kg of ferrous glycinate, 9.4kg of cerium isopropoxide, 593.78g of titanium propoxide, and 894.9g of zirconium ethoxide in 25kg of ethanol and add 300g of cationic polyacrylamide, use 1mol / L oxalic acid to adjust the pH=4.2, stir in a mechanical stirrer at room temperature for 5h, put the mixture in a hydrothermal reaction kettle for 12h at 220°C for hydrothermal synthesis reaction.
[0079] 3) Mix the slurry obtained after the hydrothermal synthesis reaction with the aluminum sol prepared in 1) and apply it on light-weight, low thermal conductivity, low heat capacity glass fiber pap...
Embodiment 2
[0081] Catalyst preparation method:
[0082] 1) Dissolve 12kg of aluminum isopropoxide in 12kg of deionized water, heat in a water bath to 85°C, and stir mechanically for 1 hour. The pH value of the solution was adjusted to 3.9 with 1 mol / L acetic acid, and the aluminum sol was prepared after stirring for 12 hours in a water bath.
[0083] 2) Dissolve 1.4kg copper citrate, 2.4kg manganese L-aspartate, 17.5kg ferrous glycinate, 12.9kg cerium isopropoxide, 1.4g propoxy titanium, 1.2g ethoxy zirconium in 25kg Add 420g of cationic polyacrylamide to ethanol, use 1mol / L oxalic acid to adjust the pH to 4.2, stir in a mechanical stirrer at room temperature for 5h, and place the mixture in a hydrothermal reactor at 220°C for 12h. synthesis reaction.
[0084] 3) Mix the slurry obtained after the hydrothermal synthesis reaction with the aluminum sol prepared in 1) and apply it on the glass fiber paper with light weight, low thermal conductivity and low heat capacity, and then press it ...
PUM
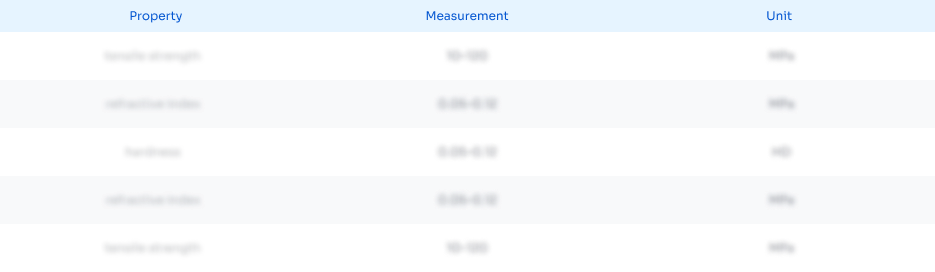
Abstract
Description
Claims
Application Information

- Generate Ideas
- Intellectual Property
- Life Sciences
- Materials
- Tech Scout
- Unparalleled Data Quality
- Higher Quality Content
- 60% Fewer Hallucinations
Browse by: Latest US Patents, China's latest patents, Technical Efficacy Thesaurus, Application Domain, Technology Topic, Popular Technical Reports.
© 2025 PatSnap. All rights reserved.Legal|Privacy policy|Modern Slavery Act Transparency Statement|Sitemap|About US| Contact US: help@patsnap.com