Full-wet process for extracting high-purity zinc from waste galvanized sheet
A galvanized sheet and all-wet process technology, which is applied in the field of all-wet process, can solve the problems of difficulty in obtaining high-purity zinc powder, high equipment requirements, and low production efficiency, and achieve low production costs, low production energy consumption, and waste little effect
- Summary
- Abstract
- Description
- Claims
- Application Information
AI Technical Summary
Problems solved by technology
Method used
Image
Examples
Embodiment 1
[0063] see figure 1 , Wash the waste galvanized sheet with water first, and then soak the waste galvanized sheet in 3% degreasing agent for 2 hours, and the solution temperature is 40°C. After degreasing, rinse with clean water once, and immerse the waste galvanized sheet in dilute sulfuric acid. The pH value of dilute sulfuric acid is about 1. The reaction time is 3 hours, and the pH value of the leaching end point is 4. Add 1.2 times the theoretical amount of industrial product hydrogen peroxide with a solute mass fraction of 30%, and stir thoroughly for 0.5 h. Then add phosphoric acid whose mass fraction of solute is 10% in an amount 1.5 times of the theoretical amount, and the reaction time is 1.0 h. After the phosphoric acid iron removal reaction is completed, the solution is filtered, and the filtrate is transported to the enrichment tank. Add 1.5 times the theoretical amount of Na to the enrichment tank 2 CO 3 Solid, and constantly stirring, the speed is 50r / min, th...
Embodiment 2
[0065] Wash the waste galvanized sheet with water first, and then soak the waste galvanized sheet in 3% degreasing agent for 2 hours, and the solution temperature is 50°C. After the degreasing is finished, rinse it once with clear water, immerse the waste galvanized sheet in dilute sulfuric acid, the pH value of dilute sulfuric acid is 1, the reaction time is 1h, and the pH value of the leaching end point is 4. Add 1.2 times the theoretical amount of industrial product hydrogen peroxide with a solute mass fraction of 30%, and stir thoroughly for 0.5 h. Then add phosphoric acid whose mass fraction of solute is 10% in an amount 1.5 times of the theoretical amount, and the reaction time is 1.0 h. After the phosphoric acid iron removal reaction is completed, the solution is filtered, and the filtrate is transported to the enrichment tank. Add 1.5 times the theoretical amount of Na to the enrichment tank 2 CO 3 Solid, and constantly stirring, the speed is 50r / min, the reaction t...
Embodiment 3
[0067] Wash the waste galvanized sheet with water first, and then soak the waste galvanized sheet in 3% degreasing agent for 2 hours, and the solution temperature is 50°C. After the degreasing is finished, rinse it once with clear water, immerse the waste galvanized sheet in dilute sulfuric acid, the pH value of dilute sulfuric acid is 1, the reaction time is 3 hours, and the pH value of the leaching end point is 4. Add 1.2 times the theoretical amount of industrial product hydrogen peroxide with a solute mass fraction of 30%, and stir thoroughly for 0.5 h. Then add phosphoric acid whose mass fraction of solute is 10% in a theoretical amount of 1.1 times, and the reaction time is 1.0 h. After the phosphoric acid iron removal reaction is completed, the solution is filtered, and the filtrate is transported to the enrichment tank. Add 1.5 times the theoretical amount of Na to the enrichment tank 2 CO 3 Solid, and constantly stirring, the speed is 50r / min, the reaction time is ...
PUM
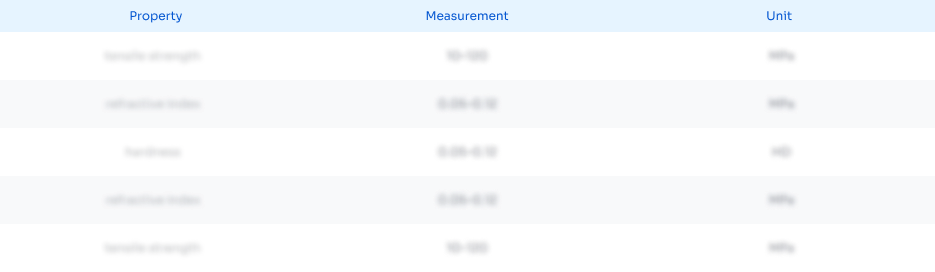
Abstract
Description
Claims
Application Information

- Generate Ideas
- Intellectual Property
- Life Sciences
- Materials
- Tech Scout
- Unparalleled Data Quality
- Higher Quality Content
- 60% Fewer Hallucinations
Browse by: Latest US Patents, China's latest patents, Technical Efficacy Thesaurus, Application Domain, Technology Topic, Popular Technical Reports.
© 2025 PatSnap. All rights reserved.Legal|Privacy policy|Modern Slavery Act Transparency Statement|Sitemap|About US| Contact US: help@patsnap.com