Preparation method of foamed ceramic material with density gradient
A technology of foamed ceramics and density gradients, applied in glass manufacturing equipment, manufacturing tools, glass molding, etc., can solve the problems of low flexural strength, fracture, high scrap rate, etc., achieve high flexural strength, reduce fracture, improve The effect of intensity
- Summary
- Abstract
- Description
- Claims
- Application Information
AI Technical Summary
Problems solved by technology
Method used
Image
Examples
specific Embodiment approach
[0029] The present invention is based on the potash feldspar-clay raw material system to prepare the foamed ceramic raw material ratio and firing temperature on the basis of its strength, porosity and thermal conductivity, and adopts the following three approaches: (1) in the cloth When selecting granulated materials with different proportions in the thickness direction and choosing the same firing temperature, the foamed glass-ceramic wall materials with different porosity, strength and thermal conductivity can be obtained. (2) When fabricating, select granulated materials with the same composition in the thickness direction, and set a temperature gradient in the height direction during firing to obtain foamed glass-ceramic walls with different porosity, strength and thermal conductivity from top to bottom. Material. (3) When fabricating, select granulated materials with different compositions in the thickness direction, and set a temperature gradient in the thickness directi...
Embodiment 1
[0047] 180-mesh potassium feldspar and 180-mesh clay were mixed in a weight ratio of 70:28 and 80:18 with 2 wt% 325-mesh silicon carbide for 2 hours using a ball mill. Use a disc granulator to granulate and granulate. After drying at 110° C. for 8 hours, use sieving to granulate balls with a diameter of 1 to 3 mm. Use mullite-cordierite as kiln furniture to build a 450×450mm space, then lay alumina fiber paper, and then lay 2cm thick potassium feldspar:clay:silicon carbide=80:18:2 granulation balls on the upper layer Lay 1cm thick potassium feldspar:clay:silicon carbide=70:28:2 granulation balls. The sample was fired in an oxidizing atmosphere in a resistance furnace at a firing temperature of 1260°C and kept for 4 hours, then cooled to 40°C with the furnace and released from the furnace to obtain a sample thickness of 5.6 cm. The properties of the sample are shown in Table 1.
[0048] Table 1 Properties of foamed glass-ceramic materials
[0049]
Embodiment 2
[0051] 180-mesh potassium feldspar and 180-mesh clay were mixed in a weight ratio of 60:38 and 70:28 with 2 wt% 325-mesh silicon carbide for 2 hours using a ball mill. Use a disc granulator to granulate and granulate. After drying at 110° C. for 8 hours, use sieving to granulate balls with a diameter of 1 to 3 mm. Using mullite-cordierite as kiln furniture, build a 450×450mm space, then lay alumina fiber paper, and then lay 2cm thick shale:clay:silicon carbide=70:28:2 granulation balls on the upper layer Put 1cm thick shale:clay:silicon carbide=60:38:2 granulation balls. The sample was fired in an oxidative atmosphere in a resistance furnace at a firing temperature of 1260°C, kept for 4 hours, then cooled to 40°C with the furnace and released from the furnace to obtain a sample thickness of 6.3cm. The properties of the sample are shown in Table 2.
[0052] Table 2 Properties of foamed glass-ceramic materials
[0053]
PUM
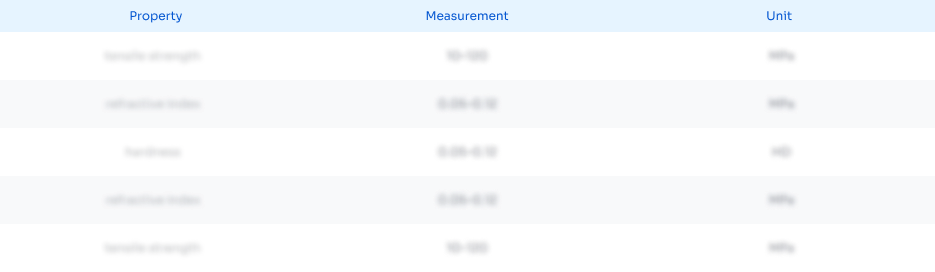
Abstract
Description
Claims
Application Information

- Generate Ideas
- Intellectual Property
- Life Sciences
- Materials
- Tech Scout
- Unparalleled Data Quality
- Higher Quality Content
- 60% Fewer Hallucinations
Browse by: Latest US Patents, China's latest patents, Technical Efficacy Thesaurus, Application Domain, Technology Topic, Popular Technical Reports.
© 2025 PatSnap. All rights reserved.Legal|Privacy policy|Modern Slavery Act Transparency Statement|Sitemap|About US| Contact US: help@patsnap.com