A method for preparing graphene high-temperature electrothermal film based on lig method
A graphene and electric heating film technology, applied in the field of preparing graphene high temperature electric heating film, can solve the problems affecting the use and promotion of graphene electric heating film, the amplification of graphene defects, the power attenuation of electric heating film, etc., to achieve excellent performance, ensure stability, very flexible effect
- Summary
- Abstract
- Description
- Claims
- Application Information
AI Technical Summary
Problems solved by technology
Method used
Examples
Embodiment 1
[0042] 1) Coat thermoplastic PI prepolymer (polyamic acid) on the surface of polyimide insulating film with a thickness of 50 microns, and dry to form a semi-cured polyamic acid film. The drying temperature is 150°C for 10 minutes;
[0043] 2) One side of the semi-cured polyamic acid film obtained in 1) was subjected to high-temperature lamination (imidization) with copper foil at a lamination temperature of 350°C for 1 h and a pressure of 5 MPa to obtain a PI-copper electrode base material;
[0044]3) On the surface of commercial PI (thickness 10 microns), pre-coat PI prepolymer and dry to form a semi-cured polyamic acid film. The drying temperature is 150 ° C for 10 minutes to form a PI-polyamic acid film material;
[0045] 4) Open holes locally on the PI-polyamic acid membrane material, and then press it with the PI-copper electrode assembly formed in 2), and complete the imidization treatment. The pressing temperature is 350°C and the time is 1h , the pressure is 5 MPa. ...
Embodiment 2
[0050] 1) On the surface of copper foil, apply thermoplastic PI prepolymer (polyamic acid) and dry to form a semi-cured polyamic acid film. The drying temperature is 150°C for 10 minutes;
[0051] 2) 1) PI insulating base material with a thickness of 50 microns was subjected to high-temperature lamination (imidization), the lamination temperature was 350 ° C, the time was 1 h, and the pressure was 5 MPa to obtain the PI-copper electrode base material;
[0052] 3) On the surface of the PI-copper electrode substrate, pre-coat PI prepolymer and dry to form a semi-cured polyamic acid film. The drying temperature is 150°C for 10 minutes to form a PI-polyamic acid film material. During this process , carry out local protection on the copper foil electrode terminal area to ensure that the surface terminal area does not cover the PI prepolymer;
[0053] 4) Complete the imidization treatment on the polyamic acid film formed in 3), the heat treatment temperature is 350°C, and the time i...
Embodiment 3
[0058] 1) On the surface of the 50 micron thick adhesive-free PI copper-clad film, a patterned copper electrode was prepared by wet etching to obtain a PI-copper electrode substrate;
[0059] 2) On the surface of commercial PI (thickness 10 microns), pre-coat PI prepolymer and dry to form a semi-cured polyamic acid film. The drying temperature is 150 ° C for 10 minutes to form a PI-polyamic acid film material;
[0060] 3) Open holes in the PI-polyamic acid membrane material, and then press it with the PI-copper electrode assembly formed in 2), and complete the imidization treatment. The pressing temperature is 350 ° C and the time is 1 h , the pressure is 5 MPa. Make sure to expose the local copper electrode terminal through the opening before pressing, so as to obtain the PI-copper electrode-PI (to-be-LIG layer) assembly.
[0061] 4) Use laser scanning equipment to induce the formation of a graphene heating layer pattern on the surface of PI, and finally form a PI-copper ele...
PUM
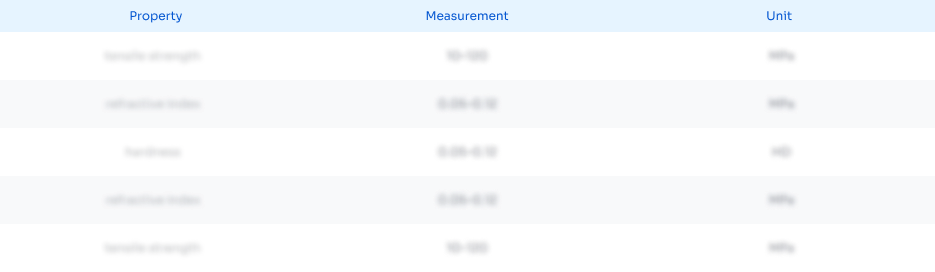
Abstract
Description
Claims
Application Information

- R&D Engineer
- R&D Manager
- IP Professional
- Industry Leading Data Capabilities
- Powerful AI technology
- Patent DNA Extraction
Browse by: Latest US Patents, China's latest patents, Technical Efficacy Thesaurus, Application Domain, Technology Topic, Popular Technical Reports.
© 2024 PatSnap. All rights reserved.Legal|Privacy policy|Modern Slavery Act Transparency Statement|Sitemap|About US| Contact US: help@patsnap.com