Heat conduction adhesion silica gel
A thermally conductive silicone sheet, silicone technology, applied in the direction of adhesives, film/sheet adhesives, non-polymer adhesive additives, etc. It can improve the basic mechanical properties, high fluidity, and enhance the thickening effect.
- Summary
- Abstract
- Description
- Claims
- Application Information
AI Technical Summary
Problems solved by technology
Method used
Image
Examples
preparation example Construction
[0034] The preparation method of the thermally conductive adhesive silica gel comprises the following steps:
[0035] S1: Pass methyl vinyl silicone rubber and simethicone oil into a mill for full grinding to prepare a base material with good fluidity, and combine the base material, silane coupling agent and fumed silica, and nitriding The silicon is uniformly mixed and then passed into the reaction kettle; firstly, dimethyl silicone oil and methyl vinyl silicone rubber are used for grinding and mixing, and then other additive components are added, which can effectively speed up the preparation process;
[0036] S2: Control the rotation speed in the reaction kettle to 380-420r / min and carry out high-speed rotation and stirring at room temperature, and add spherical alumina particles several times during the stirring process, and control the stirring time for 35-45 minutes to obtain a viscous colloid; The spherical alumina particles are added several times, and the high-speed s...
Embodiment approach
[0044] As an embodiment of the present invention, the heat dissipation holes 44 are designed in the shape of a truncated cone, and the area of the side of the heat dissipation holes 44 close to the base layer 1 is smaller than the area of the side of the heat dissipation holes 44 away from the base layer 1; conduction; when working, the heat is conducted to the heat dissipation bar 43 along the carbon fiber mesh, and through the contact between the heat dissipation bar 43 and the air, the heat dissipation effect is achieved. The setting of the heat dissipation hole 44 effectively increases the heat dissipation effect between the heat dissipation bar 43 and the air. The heat exchange area enhances the heat dissipation efficiency, and the truncated design of the heat dissipation holes 44 and the mutual conduction design of the heat dissipation holes 44 can effectively increase the air convection rate in the heat dissipation holes 44, thereby enhancing the heat dissipation rate...
PUM
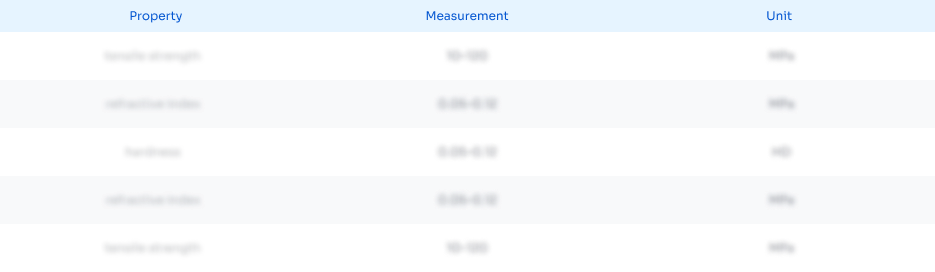
Abstract
Description
Claims
Application Information

- Generate Ideas
- Intellectual Property
- Life Sciences
- Materials
- Tech Scout
- Unparalleled Data Quality
- Higher Quality Content
- 60% Fewer Hallucinations
Browse by: Latest US Patents, China's latest patents, Technical Efficacy Thesaurus, Application Domain, Technology Topic, Popular Technical Reports.
© 2025 PatSnap. All rights reserved.Legal|Privacy policy|Modern Slavery Act Transparency Statement|Sitemap|About US| Contact US: help@patsnap.com