Manufacturing process of SMD1612 crystal resonator
A technology of SMD1612 and crystal resonator, applied in the direction of electrical components, impedance network, etc., can solve the problems of complex packaging process, high equipment investment cost, complex phase diagram of gold-tin binary alloy, etc., to reduce costs, avoid product loss, Reliable and stable sealing effect
- Summary
- Abstract
- Description
- Claims
- Application Information
AI Technical Summary
Problems solved by technology
Method used
Image
Examples
Embodiment Construction
[0024] The present invention is described in further detail now in conjunction with accompanying drawing. These drawings are all simplified schematic diagrams, which only illustrate the basic structure of the present invention in a schematic manner, so they only show the configurations related to the present invention.
[0025] Such as figure 1 Shown, a kind of manufacturing process of SMD1612 crystal resonator comprises the following steps:
[0026] Pre-washing→arraying→post-washing→coating→glue dispensing→curing→fine-tuning→seal welding→aging→reflow soldering→leak detection→test printing taping→packaging→storage;
[0027] In the wafer arrangement step: the length of the wafer is 1.04-1.1mm, and the width of the wafer is 0.64-0.85mm;
[0028] In the glue dispensing step: use the cut-in method to load the chip, the chip loading position is controlled at 1 / 2 to 1 / 3 of the primer, and the chip angle when loading and cutting is 1-3 degrees;
[0029] In the fine-tuning step: th...
PUM
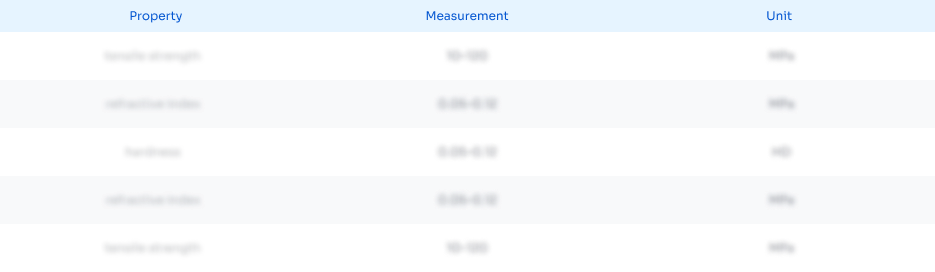
Abstract
Description
Claims
Application Information

- Generate Ideas
- Intellectual Property
- Life Sciences
- Materials
- Tech Scout
- Unparalleled Data Quality
- Higher Quality Content
- 60% Fewer Hallucinations
Browse by: Latest US Patents, China's latest patents, Technical Efficacy Thesaurus, Application Domain, Technology Topic, Popular Technical Reports.
© 2025 PatSnap. All rights reserved.Legal|Privacy policy|Modern Slavery Act Transparency Statement|Sitemap|About US| Contact US: help@patsnap.com