Railway wagon lower pull rod breaking fault detection method based on deep learning
A railway freight car and deep learning technology, applied in the field of image recognition, can solve the problems of low detection accuracy and detection efficiency, achieve safe and efficient operation, improve detection efficiency, and ensure detection accuracy
- Summary
- Abstract
- Description
- Claims
- Application Information
AI Technical Summary
Problems solved by technology
Method used
Image
Examples
specific Embodiment approach 1
[0020] Specific implementation mode 1. Combination figure 1 This embodiment will be described. A deep learning-based method for detecting the breakage of the lower rod of a railway freight car described in this embodiment, the method is specifically implemented through the following steps:
[0021] Step 1. Collect the image of the visual parts of the truck through the image acquisition equipment arranged at the detection station, and save the collected image in a designated location;
[0022] Step 2. After reading the collected image from the designated position, roughly locate the area of the pull-down rod in the collected image, and intercept the sub-image of the location of the pull-down rod;
[0023] Step 3. Perform data amplification processing on the sub-image at the location of the intercepted pull-down rod, and then mark the image obtained by the data amplification processing to obtain a training data set;
[0024] Step 4, input the obtained training data set into ...
specific Embodiment approach 2
[0034] Embodiment 2. This embodiment differs from Embodiment 1 in that: after the sub-picture where the pull-down rod is located is cut out in step 2, the background color of the sub-picture where the pull-down rod is located is set to white.
[0035] In this embodiment, in order to eliminate the interference of the background around the pull-down rod on the detection of the broken position, after obtaining the sub-image of the location of the pull-down rod, the background color near the pull-down rod is set to white to reduce the interference information for identification.
specific Embodiment approach 3
[0036] Specific Embodiment 3. The difference between this embodiment and specific embodiment 2 is: the data amplification processing is performed on the intercepted sub-picture at the location of the pull-down bar, and the data amplification method adopted includes image rotation and image random cropping. , image horizontal flip, image vertical flip, image stretch and image zoom.
PUM
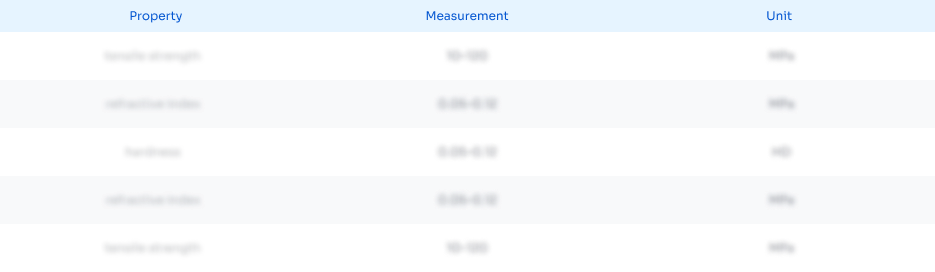
Abstract
Description
Claims
Application Information

- R&D
- Intellectual Property
- Life Sciences
- Materials
- Tech Scout
- Unparalleled Data Quality
- Higher Quality Content
- 60% Fewer Hallucinations
Browse by: Latest US Patents, China's latest patents, Technical Efficacy Thesaurus, Application Domain, Technology Topic, Popular Technical Reports.
© 2025 PatSnap. All rights reserved.Legal|Privacy policy|Modern Slavery Act Transparency Statement|Sitemap|About US| Contact US: help@patsnap.com