Aluminum alloy deironing method
A technology of aluminum alloy and iron remover, which is applied in the field of iron removal of aluminum alloy, can solve the problems of difficult reaction control, unsuitability for industrial production, and difficult operation in the iron removal process, so as to improve the efficiency of slag removal, less harmful gas and low cost Effect
- Summary
- Abstract
- Description
- Claims
- Application Information
AI Technical Summary
Problems solved by technology
Method used
Image
Examples
Embodiment 1
[0032] Such as figure 1 Shown, a kind of aluminum alloy iron removal method comprises the steps:
[0033] Step 1, weighing the refining agent, die-casting into blocks and baking:
[0034] Weigh an aluminum block with a mass of 10kg, weigh 20g of refining agent, die-cast the refining agent into a refining agent block, put the refining agent block in an oven, raise the temperature of the oven to 250°C and keep it warm for 60 minutes; the AlF in the refining agent 3 、Na 2 SO 4 、Na 2 AlF 6 、C 2 Cl 6 The mass-number ratio with C powder is 2.75:7.2:6.5:3.25:1.
[0035] Step 2, weigh the modifier and bake:
[0036] Take by weighing 40g of the aluminum-chromium master alloy modifier, put the aluminum-chromium master alloy modifier in the oven, make the temperature of the oven rise to 200°C and keep it warm for 40min; the amount of chromium in the aluminum-chromium master alloy modifier in the modifier The content is 9%.
[0037] Step 3, weigh the iron remover and bake it:
...
Embodiment 2
[0049] A method for removing iron from an aluminum alloy, comprising the steps of:
[0050] Step 1, weighing the refining agent, die-casting into blocks and baking:
[0051] Weigh an aluminum block with a mass of 10kg, weigh 35g of refining agent, die-cast the refining agent into a refining agent block, put the refining agent block in an oven, raise the temperature of the oven to 350°C and keep it warm for 90 minutes; the AlF in the refining agent 3 、Na 2 SO 4 、Na 2 AlF 6 、C 2 Cl 6 The mass-number ratio with C powder is 7.25:8:8.5:4.25:1.5.
[0052] Step 2, weigh the modifier and bake:
[0053] Take by weighing 60g of the aluminum-chromium master alloy modifier, put the aluminum-chromium master alloy modifier in the oven, make the temperature of the oven rise to 300°C and keep it warm for 70min; the amount of chromium in the aluminum-chromium master alloy modifier in the modifier The content is 11%.
[0054] Step 3, weigh the iron remover and bake it:
[0055] Weigh ...
Embodiment 3
[0065] A method for removing iron from an aluminum alloy, comprising the steps of:
[0066] Step 1, weighing the refining agent, die-casting into blocks and baking:
[0067] Weigh an aluminum block with a mass of 10kg, weigh 30g of refining agent, die-cast the refining agent into a refining agent block, put the refining agent block in an oven, raise the temperature of the oven to 300°C and keep it warm for 75 minutes; the AlF in the refining agent 3 、Na 2 SO 4 、Na 2 AlF 6 、C 2 Cl 6 The mass-number ratio with C powder is 5.25:7.5:7.5:3.85:1.25.
[0068] Step 2, weigh the modifier and bake:
[0069] Take by weighing 50g of the aluminum-chromium master alloy modifier, put the aluminum-chromium master alloy modifier in the oven, make the temperature of the oven rise to 250°C and keep it warm for 55min; the amount of chromium in the aluminum-chromium master alloy modifier in the modifier The content is 10%.
[0070] Step 3, weigh the iron remover and bake it:
[0071] Wei...
PUM
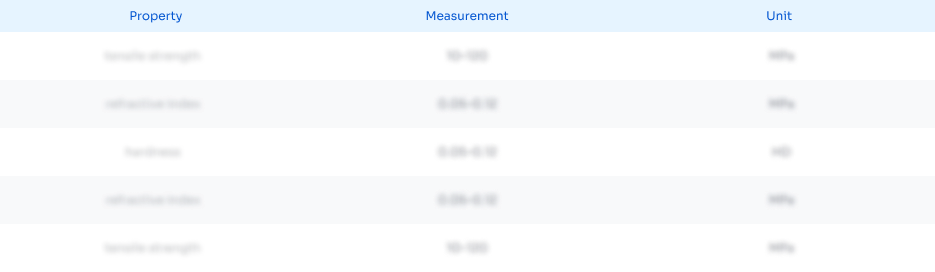
Abstract
Description
Claims
Application Information

- R&D Engineer
- R&D Manager
- IP Professional
- Industry Leading Data Capabilities
- Powerful AI technology
- Patent DNA Extraction
Browse by: Latest US Patents, China's latest patents, Technical Efficacy Thesaurus, Application Domain, Technology Topic, Popular Technical Reports.
© 2024 PatSnap. All rights reserved.Legal|Privacy policy|Modern Slavery Act Transparency Statement|Sitemap|About US| Contact US: help@patsnap.com