Saloon car brake pad with composite fibers and preparation method and application thereof
A technology of composite fibers and brake pads, applied in the field of brake pads, can solve problems such as high costs, and achieve the effects of reducing costs, enhancing adhesion, and improving interface connection.
- Summary
- Abstract
- Description
- Claims
- Application Information
AI Technical Summary
Problems solved by technology
Method used
Image
Examples
preparation example Construction
[0036] In the second aspect, the preparation method of the above-mentioned car brake pad with composite fibers, the specific steps are:
[0037] ZnNb 2 o 6 , potassium titanate whiskers, and magnesium sulfate are mixed for wet ball milling to obtain a ball-milled mixture;
[0038] mixing polyacrylonitrile fibers, silicon carbide fibers, sepiolite fibers and rabbit hair with water to obtain a premix, then adding a silane coupling agent for mixing, and drying to obtain a dried mixture;
[0039] mixing the polyhydroxyethyl methacrylate micropowder with the ball-milled mixture and the dried mixture to obtain the final mixture;
[0040] Add the modified oil and the final mixture to the abrasive tool for molding and hot pressing to obtain molded products;
[0041] The surface of the molded product is coated with abrasive, and then vulcanized to eliminate thermal stress to obtain a brake pad.
[0042] In some embodiments of the present invention, the ball milling speed in the bal...
Embodiment 1
[0053] A preparation process for a car brake pad with composite fibers, characterized in that it comprises the following steps:
[0054] S1: Weigh 12 parts of ZnNb by weight percentage 2 o 6 , 8 parts of potassium titanate whiskers and 1 part of magnesium sulfate, using absolute ethanol as a solvent, ball milled for 6 hours, poured into a round dish for drying, and passed through an 80-mesh sieve;
[0055] S2: Weigh 10 parts of polyacrylonitrile fiber, 6 parts of silicon carbide fiber, 3 parts of sepiolite fiber and 1 part of rabbit hair by weight percentage, and use deionized water as a solvent, put it into a mixer and stir for 30 minutes;
[0056] S3: Add 1 part of methyltrichlorosilane coupling agent to the obtained product of S2, continue stirring for 20 minutes, and dry;
[0057] S4: Weigh 45 parts of polyhydroxyethyl methacrylate micropowder by weight percentage, mix it with S1 and S3 results, put it into a mixer and stir for 10 minutes, and the stirring speed is 120r / ...
Embodiment 2
[0063] A preparation process for a car brake pad with composite fibers, characterized in that it comprises the following steps:
[0064] S1: Weigh 16 parts of ZnNb by weight percentage 2 o 6 12 parts of potassium titanate whiskers and 5 parts of magnesium sulfate, using absolute ethanol as a solvent, ball milling for 8 hours, pouring into a round dish to dry, passing through a 200-mesh sieve;
[0065] S2: Weigh 14 parts of polyacrylonitrile fiber, 10 parts of silicon carbide fiber, 5 parts of sepiolite fiber and 3 parts of rabbit hair by weight percentage, and use deionized water as a solvent, put it into a mixer and stir for 60 minutes;
[0066] S3: Add 2 parts of n-octyltrimethoxysilane coupling agent to the obtained product of S2, continue stirring for 40 minutes, and dry;
[0067] S4: Weigh 55 parts of polyhydroxyethyl methacrylate micropowder by weight percentage, mix it with S1 and S3 results, put it into a mixer and stir for 15 minutes, and the stirring speed is 150r / ...
PUM
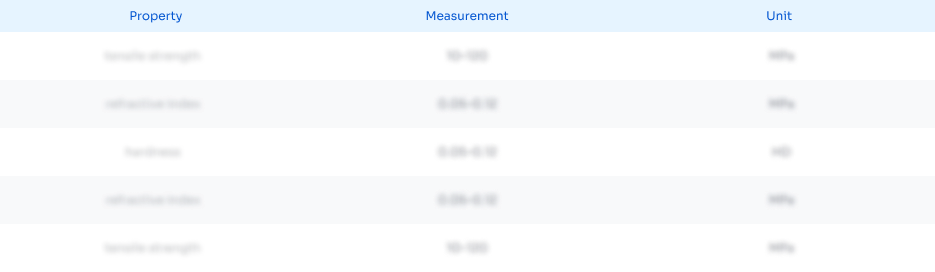
Abstract
Description
Claims
Application Information

- R&D
- Intellectual Property
- Life Sciences
- Materials
- Tech Scout
- Unparalleled Data Quality
- Higher Quality Content
- 60% Fewer Hallucinations
Browse by: Latest US Patents, China's latest patents, Technical Efficacy Thesaurus, Application Domain, Technology Topic, Popular Technical Reports.
© 2025 PatSnap. All rights reserved.Legal|Privacy policy|Modern Slavery Act Transparency Statement|Sitemap|About US| Contact US: help@patsnap.com