Wear-resistant layer production process for flow passage component of cutter-suction dredger
A technology for cutter suction dredger and overcurrent components, which is applied in the field of ship dredging, can solve the problems of increasing the downtime of dredgers, increasing replacement and maintenance costs of spare parts, etc., so as to save materials, ship repair time, and improve repairs Efficiency and the effect of reducing the amount of work
- Summary
- Abstract
- Description
- Claims
- Application Information
AI Technical Summary
Problems solved by technology
Method used
Image
Examples
Embodiment Construction
[0027] Such as Figure 1-Figure 3 As shown, the present invention provides a process for producing a wear-resistant layer for flow-through parts of a cutter suction dredger, which includes the following steps:
[0028] S1. Preparation of wear-resistant block 1, which includes:
[0029] S101. Cut the No. 45 steel plate into several trapezoidal steel plates according to the required size, and cut the corners of each trapezoidal steel plate vertically. Among them, No. 45 steel is made of No. 45 steel with a low phosphorus flow residual value. The cut length at each corner of the trapezoidal steel plate is 80%-90% of the thickness of the trapezoidal steel plate, and the cutting angle is 45°.
[0030] S102: Anneal the cut trapezoidal steel plate, heat the trapezoidal steel plate to 900°C, keep it for 2 hours, and cool it naturally to room temperature.
[0031] S103. Punch positioning hole 2 on the center of each trapezoidal steel plate after annealing treatment. Use a 60mm drill bit to re...
PUM
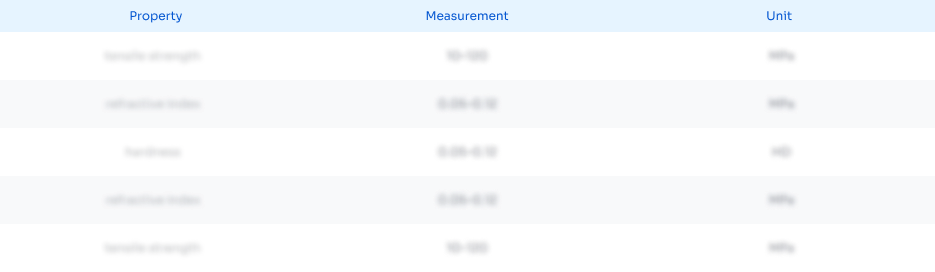
Abstract
Description
Claims
Application Information

- R&D
- Intellectual Property
- Life Sciences
- Materials
- Tech Scout
- Unparalleled Data Quality
- Higher Quality Content
- 60% Fewer Hallucinations
Browse by: Latest US Patents, China's latest patents, Technical Efficacy Thesaurus, Application Domain, Technology Topic, Popular Technical Reports.
© 2025 PatSnap. All rights reserved.Legal|Privacy policy|Modern Slavery Act Transparency Statement|Sitemap|About US| Contact US: help@patsnap.com