Preparation process of zirconium oxide composite abrasive, and grinding fluid
A preparation process and composite abrasive technology, which is applied to polishing compositions containing abrasives, other chemical processes, chemical instruments and methods, etc., can solve the problems of increased flatness error of silicon wafers, low surface residual stress, and decreased grinding efficiency.
- Summary
- Abstract
- Description
- Claims
- Application Information
AI Technical Summary
Problems solved by technology
Method used
Image
Examples
Embodiment 1
[0045] In the present embodiment, the preparation technology of zirconia composite abrasive comprises the following steps:
[0046] Step 1: Preparation of zirconia composite abrasive organic precursor sol
[0047] First weigh an appropriate amount of ZrOCl 2 powder, then press ZrOCl 2 : Absolute ethanol mass ratio 1:9 Weigh an appropriate amount of absolute ethanol, pour the weighed absolute ethanol into the container, and add the weighed ZrOCl under the stirring condition of 1000-2000 rpm 2 powder, stirred for 2 hours to obtain ZrOCl 2 absolute ethanol solution.
[0048] ZrOCl 2 The dehydrated ethanol solution and aluminum isopropoxide weighed ZrOCl respectively by mass ratio 95:5 2 Anhydrous ethanol solution and aluminum isopropoxide, the two liquids were mixed under the stirring condition of 2000 rpm, and stirred for 1 hour to obtain the first mixed solution. Weigh the high-hydroxy acrylic resin (molecular weight: 4000) according to 5% of the mass of the first mixed ...
PUM
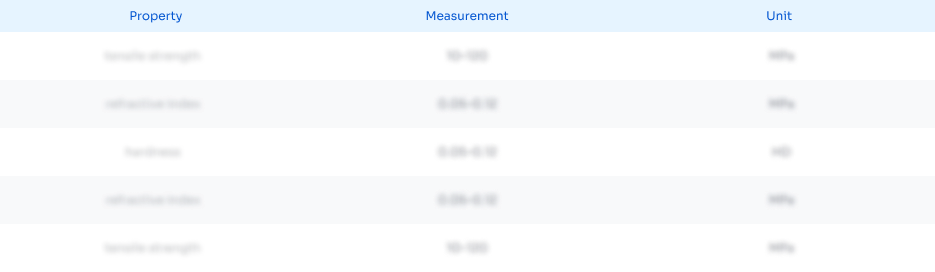
Abstract
Description
Claims
Application Information

- R&D Engineer
- R&D Manager
- IP Professional
- Industry Leading Data Capabilities
- Powerful AI technology
- Patent DNA Extraction
Browse by: Latest US Patents, China's latest patents, Technical Efficacy Thesaurus, Application Domain, Technology Topic, Popular Technical Reports.
© 2024 PatSnap. All rights reserved.Legal|Privacy policy|Modern Slavery Act Transparency Statement|Sitemap|About US| Contact US: help@patsnap.com