Low-cost low-temperature plastic dipping PVC glove forming process method
A molding process, low-cost technology, applied in the direction of household components, applications, coatings, etc., can solve the problems of complex glove molding process conditions, low decomposition temperature of polyvinyl chloride, and inability to mold by dipping, so as to improve the production and working environment and conditions, good light resistance and stability, not easy to yellow and powder
- Summary
- Abstract
- Description
- Claims
- Application Information
AI Technical Summary
Problems solved by technology
Method used
Examples
Embodiment 1
[0026] The first step is to prepare the chloroether resin modified paste:
[0027]65 parts by weight of polyvinyl chloride, 24 parts by weight of polytrimethylene adipate, 53 parts by weight of chloroether resin, and 0.5 parts by weight of dibenzoyl peroxide were mixed at a low speed, then dispersed for 5 hours under high-speed stirring, and then added 4 parts by weight of nepheline syenite powder, 4 parts by weight of titanium dioxide, 17 parts by weight of viscosity reducer cyclohexane 1,2-diisooctyl carboxylate and 5 parts by weight of thixotropic agent sericite powder, 4000rpm / min rotating speed Disperse evenly and use it to make the modified paste of chloroether resin; the second step, the preparation of allyl resin prepolymer microcapsules: 24 parts by weight of ethylene glycol dicarbonate diallyl are dispersed in 31 parts by weight 1,000,000,000,000,000,000,000,000,000,0,0,0,0,0,0,0,0,0,0 and 1,0,000,000,000,000,000,0,0,0,0,0,0,0,0,0,0,0,0,0,0,0,0,0,0,0,0,0,0,0,0,0,, an...
Embodiment 2
[0029] The first step, the preparation of allyl resin prepolymer microcapsules: disperse 24 parts by weight of allyl resin in 25 parts by weight of xylene, add 14 parts of chloroether resin to obtain A solution, then add 0.1 parts by weight of water-soluble Initiator potassium persulfate and 0.1 weight part of emulsifier octylphenol polyoxyethylene ether maleic acid monoester are dissolved in 20 weight parts of water to obtain B solution, B solution and A solution are mixed, at 10000rpm / minute high shear Stir in an emulsifier at 75°C for 10 minutes, then stir at a low speed of 100rpm / min for 2 minutes, remove xylene, filter, and dry at 45°C for 24 hours to obtain propylene-based resin prepolymer microcapsules; the second step is to prepare chlorine Ether resin modified paste: 17 parts by weight of polyester plasticizer polytrimethylene sebacate, 58 parts by weight of polyvinyl chloride, 49 parts by weight of chloroether resin, and 0.1 part by weight of azobisisobutyronitrile we...
PUM
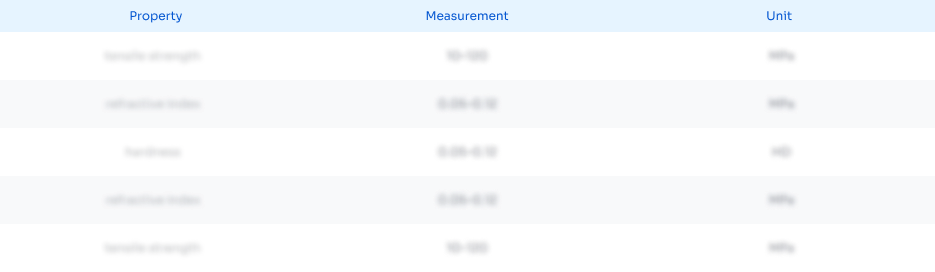
Abstract
Description
Claims
Application Information

- Generate Ideas
- Intellectual Property
- Life Sciences
- Materials
- Tech Scout
- Unparalleled Data Quality
- Higher Quality Content
- 60% Fewer Hallucinations
Browse by: Latest US Patents, China's latest patents, Technical Efficacy Thesaurus, Application Domain, Technology Topic, Popular Technical Reports.
© 2025 PatSnap. All rights reserved.Legal|Privacy policy|Modern Slavery Act Transparency Statement|Sitemap|About US| Contact US: help@patsnap.com