Preparing method and application of Cr-Al-C series MAX phase coating
A coating, cr-c technology, applied in the field of preparation of Cr-Al-C MAX phase coating, can solve problems affecting battery power, stability and life, achieve excellent corrosion resistance and protection performance, and improve the degree of bonding , Improve the effect of interface conductivity
- Summary
- Abstract
- Description
- Claims
- Application Information
AI Technical Summary
Problems solved by technology
Method used
Image
Examples
Embodiment 1
[0038] In this embodiment, the substrate is a 304 stainless steel bipolar plate used in a proton exchange membrane fuel cell, and the preparation method of the Cr-Al-C system MAX phase coating on the surface of the substrate is as follows:
[0039] (1) Put the substrate after cleaning, degreasing and drying into the cavity, and wait until the vacuum pressure in the cavity is 3.0×10 -5 Below Torr, 100 standard milliliters / minute of argon gas is introduced into the vacuum chamber, the linear anode ion source current is set to 0.3A, the substrate bias voltage is -100V, and the substrate is etched for 30 minutes with ionized argon ions.
[0040] (3) The Cr-C transition layer is deposited by arc ion plating technology, wherein the cathode arc target provides the Cr source, and the gas CH 4 Provide C source, arc target current is 90A, CH 4 The flow rate is 10 standard ml / min, the flow rate of argon gas is 300 standard ml / min, the bias voltage of the substrate is -200V, the deposition...
Embodiment 2
[0055] In this embodiment, the substrate is a 316L stainless steel bipolar plate used in a proton exchange membrane fuel cell, and the preparation method of the Cr-Al-C system MAX phase coating on the surface of the substrate is as follows:
[0056] (1) Put the 316L stainless steel substrate after cleaning, degreasing and drying into the cavity, and wait until the vacuum pressure in the cavity is 3.0×10 -5 Below Torr, 100 standard milliliters / minute of argon gas is fed into the vacuum chamber, the linear anode ion source current is set to 0.3A, the substrate bias voltage is -200V, and the substrate is etched with ionized argon ions for 20 minutes.
[0057] (2) The Cr-C transition layer is deposited by arc ion plating technology, wherein the cathode arc target provides the Cr source, and the gas CH 4 Provide C source, arc target current is 65A, CH 4 The flow rate is 10 standard ml / min, the flow rate of argon gas is 300 standard ml / min, the bias voltage of the substrate is -200...
Embodiment 3
[0061] In this embodiment, the substrate is a 309 stainless steel bipolar plate used in a proton exchange membrane fuel cell, and the preparation method of the Cr-Al-C system MAX phase coating on the surface of the substrate is as follows:
[0062] (1) Put the 309 stainless steel substrate after cleaning, degreasing and drying into the cavity, and wait until the vacuum pressure in the cavity is 3.0×10 - 5 Below Torr, 100 standard milliliters / min of argon gas was introduced into the vacuum chamber, the linear anode ion source current was set to 0.3A, the substrate bias was -150V, and the substrate was etched for 30 minutes with ionized argon ions.
[0063] (3) The Cr-C transition layer is deposited by arc ion plating technology, wherein the cathode arc target provides the Cr source, and the gas CH 4 Provide C source, arc target current is 90A, CH 4 The flow rate is 10 standard ml / min, the flow rate of argon gas is 300 standard ml / min, the bias voltage of the substrate is -150...
PUM
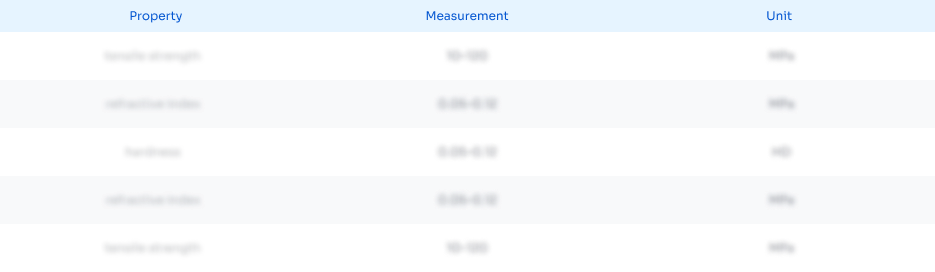
Abstract
Description
Claims
Application Information

- Generate Ideas
- Intellectual Property
- Life Sciences
- Materials
- Tech Scout
- Unparalleled Data Quality
- Higher Quality Content
- 60% Fewer Hallucinations
Browse by: Latest US Patents, China's latest patents, Technical Efficacy Thesaurus, Application Domain, Technology Topic, Popular Technical Reports.
© 2025 PatSnap. All rights reserved.Legal|Privacy policy|Modern Slavery Act Transparency Statement|Sitemap|About US| Contact US: help@patsnap.com