Purification method of copper electrolyte
A copper electrolyte and electrolyte technology, applied in the field of metallurgy, can solve the problems of high loss, time-consuming and laborious, and poor stability of resin impurity removal by concentration method.
- Summary
- Abstract
- Description
- Claims
- Application Information
AI Technical Summary
Problems solved by technology
Method used
Image
Examples
Embodiment 1
[0045] Take Cu 2+ Concentration is 100g / L waste copper nitrate electrolyte 40L, after heating to electrolyte temperature 35 ℃, add 500 meshes of purified copper powder (100*the amount of (As+Sb+Bi+Pb+Ag) in the solution) 464g, cycle Electrowinning was carried out after 6 hours of reaction, and the current density was controlled to be 150A / m 2 , the electrodeposition temperature is 35°C, and the electrodeposition time is 24h.
[0046] Electrolyte composition after purification in the embodiment of the present invention 1 in table 1
[0047] name Electrolyte (before electrowinning) Electrolyte (12h after electrowinning) Electrolyte (24h after electrowinning) Cu 2+ / g / L
102 90.4 81.5 HNO 3 / g / L
4.2 9.2 13.4 Ag / mg / L 5 <0.5
<0.5
As / mg / L 20 10 9.3 Sb / mg / L 15 9 8.1 Bi / mg / L 16 8 7.5 Pb / mg / L 60 40 38
[0048] Content of cathode copper element in table 2 embodiment 1 of the present invention
[00...
Embodiment 2
[0051] Take Cu 2+ 40L of copper nitrate electrolyte with a concentration of 150g / L, heated to the temperature of the electrolyte at 30°C, and then adding 579.6g of 600-mesh copper powder (the amount of (As+Sb+Bi+Pb+Ag) in the 115* solution) to control the current The density is 150A / m 2 , the electrodeposition temperature is 30°C, and the electrodeposition time is 24h.
[0052] Electrolyte composition after purification in the embodiment of the present invention 2 in table 3
[0053] name Electrolyte (before electrowinning) Electrolyte (12h after electrowinning) Electrolyte (24h after electrowinning) Cu 2+ / g / L
152 128.3 113.2 HNO 3 / g / L
8.5 14.1 18.6 Ag / mg / L 8 <0.5
<0.5
As / mg / L 22 9.8 9.0 Sb / mg / L 17 8.7 7.9 Bi / mg / L 17 7.8 7.3 Pb / mg / L 62 40 37
[0054] Content of cathode copper element in table 4 embodiment 2 of the present invention
[0055] Cu% Ag% S% Fe% Pb% As% S...
Embodiment 3
[0057] Take Cu 2+ Two parts of 40L of copper nitrate electrolyte with a concentration of 100g / L were heated to the temperature of the electrolyte at 33°C, and copper powder of 500 mesh and 1000 mesh were added respectively (110*the amount of (As+Sb+Bi+Pb+Ag) in the solution )510.4g, the control current density is 160A / m 2 , the electrodeposition temperature is 33°C, and the electrodeposition time is 24h.
[0058] Electrolyte composition after purification in different granularity embodiments of table 5
[0059]
[0060] Cathode copper element content in different particle size embodiments of table 6
[0061]
[0062]
PUM
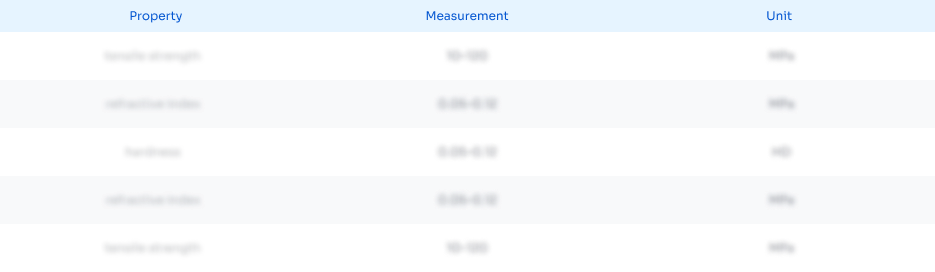
Abstract
Description
Claims
Application Information

- R&D Engineer
- R&D Manager
- IP Professional
- Industry Leading Data Capabilities
- Powerful AI technology
- Patent DNA Extraction
Browse by: Latest US Patents, China's latest patents, Technical Efficacy Thesaurus, Application Domain, Technology Topic, Popular Technical Reports.
© 2024 PatSnap. All rights reserved.Legal|Privacy policy|Modern Slavery Act Transparency Statement|Sitemap|About US| Contact US: help@patsnap.com