Method for preparing thermoplastic boron phenolic resin by solid-phase synthesis method
A technology of boron phenolic resin and solid-phase synthesis, which is applied in the field of polymer material preparation, can solve the problems of reducing resin crosslinking density, poor modification effect, and difficult hydrolysis, etc., and achieves excellent heat resistance and mechanical properties. Synthesis The process is mild and controllable, and the effect of increasing the molecular weight of the product
- Summary
- Abstract
- Description
- Claims
- Application Information
AI Technical Summary
Problems solved by technology
Method used
Image
Examples
Embodiment 1
[0019] Prepare materials according to the mass ratio of phenol:boric acid:hydrochloric acid:cyclohexane=1:0.4:0.03:0.1 and the molar ratio of phenol:paraformaldehyde=1:1.1, and melt the phenol into a liquid state at 50°C. In a reaction kettle equipped with a stirring device, a thermocouple, a heating device, and a water separator, add phenol, boric acid, hydrochloric acid, and cyclohexane according to the above ratio, stir and raise the temperature to 190°C to stop the reaction, and discharge the generated water in time during the reaction. After the reaction, the cyclohexane was distilled off. When the system is cooled to 90°C, add paraformaldehyde in small amounts several times, and keep stirring. After the addition is completed, the temperature is raised to 110°C to continue the reaction for 1 hour. The obtained viscous resin was vacuum-dried at 160°C for 1 hour, cooled to room temperature, and the obtained light yellow or yellow-green transparent solid was thermoplastic bo...
Embodiment 2
[0021] Prepare materials according to the mass ratio of o-cresol: boric acid: sulfuric acid: xylene = 1:0.2:0.01:0.4 and the molar ratio of o-cresol: paraformaldehyde = 1:1, and melt the o-cresol into a liquid state at 60°C. In a three-neck flask equipped with a stirrer, a thermometer and a glass water separator, add o-cresol, boric acid, sulfuric acid and xylene according to the above ratio, stir and heat up to 200°C to stop the reaction, and discharge the generated water in time during the period, and the reaction is over. Post-distillation to remove xylene. When the system was cooled to 50°C, paraformaldehyde was added in small amounts several times, and the stirring was continued. After the addition was completed, the temperature was raised to 100°C to continue the reaction for 1 hour. The obtained viscous resin was vacuum-dried at 130° C. for 1 hour, cooled to room temperature, and the obtained light yellow or yellow-green transparent solid was thermoplastic boron phenoli...
Embodiment 3
[0023] Prepare materials according to the mass ratio of phenol:boric acid:oxalic acid:toluene=1:0.25:0.01:0.3 and the molar ratio of phenol:paraformaldehyde=1:0.95, and melt the phenol into a liquid state at 60°C. In a three-neck flask equipped with a stirrer, a thermometer and a glass water separator, add phenol, boric acid, oxalic acid and toluene according to the above ratio, stir and raise the temperature to 180°C to stop the reaction, and discharge the generated water in time during the period. Toluene was distilled off. When the system was cooled to 70°C, paraformaldehyde was added in small amounts several times, and the stirring was continued. After the addition was completed, the temperature was raised to 105°C to continue the reaction for 2 hours. The obtained viscous resin was vacuum-dried at 140°C for 30 minutes, cooled to room temperature, and the obtained light yellow or yellow-green transparent solid was thermoplastic boron phenolic resin.
[0024] The infrared ...
PUM
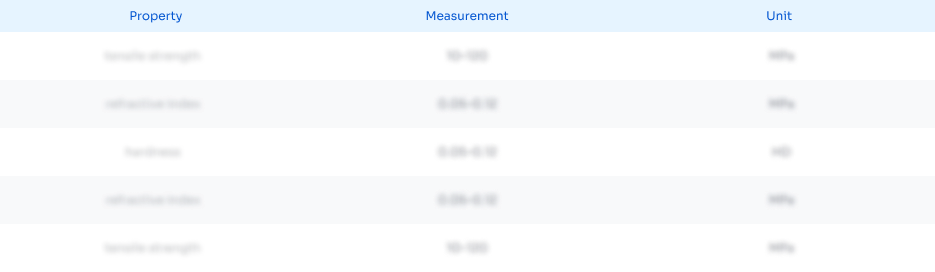
Abstract
Description
Claims
Application Information

- Generate Ideas
- Intellectual Property
- Life Sciences
- Materials
- Tech Scout
- Unparalleled Data Quality
- Higher Quality Content
- 60% Fewer Hallucinations
Browse by: Latest US Patents, China's latest patents, Technical Efficacy Thesaurus, Application Domain, Technology Topic, Popular Technical Reports.
© 2025 PatSnap. All rights reserved.Legal|Privacy policy|Modern Slavery Act Transparency Statement|Sitemap|About US| Contact US: help@patsnap.com