Method for treating NOx waste gas in preparation process of molecular sieve catalyst
A technology of preparation process and treatment method, which is applied in the field of NOx exhaust gas treatment in the preparation process of molecular sieve catalyst, can solve the problems of untargeted research reports on exhaust gas treatment methods, unsuitable for large-scale industrial application, secondary pollution of reaction products, etc., and achieves high efficiency The effect of mass transfer and micro-mixing performance, improving conversion rate and selectivity, and low maintenance frequency
- Summary
- Abstract
- Description
- Claims
- Application Information
AI Technical Summary
Problems solved by technology
Method used
Image
Examples
Embodiment 1
[0029] NO in the preparation process of a molecular sieve catalyst x The treatment method of waste gas comprises the following steps:
[0030] 1) Preparation of absorbent: the concentration of 5.0wt.% urea and 1.0wt.% KMnO 4 Mix and prepare an absorbent with a concentration of 6.0wt.%, the temperature of the absorbent is 20°C, and put the absorbent into the liquid storage tank 5 for standby;
[0031] 2) open the supergravity reactor 3, the rotor speed of the supergravity reactor 3 is set to 4000rpm; the supergravity reactor 3 is a countercurrent type;
[0032] 3) introduce absorbent: the absorbent in the liquid storage tank 5 is 3 The flow rate of / h is introduced in the supergravity reactor 3 by the liquid phase inlet 4 of the supergravity reactor 3;
[0033] 4) Remove NO x : The flow rate generated during the preparation of the molecular sieve catalyst is 100000m 3 / h, temperature is 100℃, NO x NO concentration of 3000ppm x Exhaust gas passes through NO x Exhaust gas o...
Embodiment 2
[0036] NO in the preparation process of a molecular sieve catalyst x The treatment method of waste gas comprises the following steps:
[0037] 1) Preparation of absorbent: the concentration of 50.0wt.% urea and 20.0wt.% KMnO 4 Mix and prepare an absorbent with a concentration of 70.0wt.%; set the temperature of the absorbent to 75°C and put it into the liquid storage tank 5 for standby;
[0038] 2) open the supergravity reactor 3, the rotor speed of the supergravity reactor 3 is set to 4000rpm; the supergravity reactor 3 is a countercurrent type;
[0039] 3) Introduce absorbent: the absorbent in the liquid storage tank 5 is passed through the circulating pump 6 at a rate of 500m 3 The flow rate of / h is introduced into the supergravity reactor 3 from the liquid phase inlet 4 of the supergravity reactor 3, and the absorbent flows from the inner edge of the rotor to the outer edge of the rotor at a high speed under the centrifugal force of the supergravity reactor 3, and then ...
Embodiment 3
[0043] NO in the preparation process of a molecular sieve catalyst x The treatment method of waste gas comprises the following steps:
[0044] 1) Preparation of absorbent: the concentration of 45.0wt.% urea and 1.0wt.% KMnO 4 Mix and prepare an absorbent with a concentration of 46.0wt.%; set the temperature of the absorbent to 32°C and put it into the liquid storage tank 5 for standby;
[0045] 2) Open the supergravity reactor 3, and the rotor speed of the supergravity reactor 3 is set to 1580rpm; the supergravity reactor 3 is a downstream type;
[0046] 3) Introducing the absorbent: the absorbent in the liquid storage tank 5 is passed through the circulation pump 6 at a rate of 350m 3 The flow rate of / h is introduced into the supergravity reactor 3 from the liquid phase inlet 4 of the supergravity reactor 3, and the absorbent flows from the inner edge of the rotor to the outer edge of the rotor at a high speed under the centrifugal force of the supergravity reactor 3, and ...
PUM
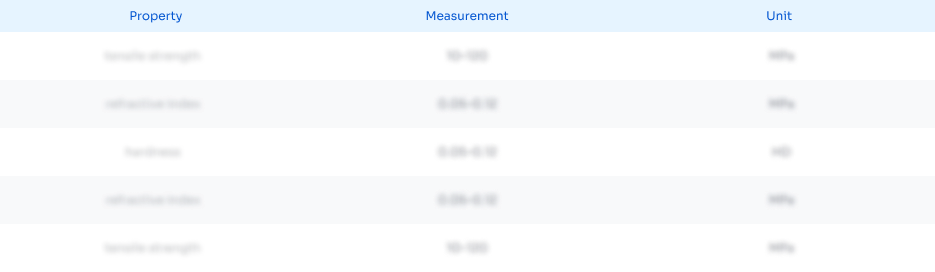
Abstract
Description
Claims
Application Information

- Generate Ideas
- Intellectual Property
- Life Sciences
- Materials
- Tech Scout
- Unparalleled Data Quality
- Higher Quality Content
- 60% Fewer Hallucinations
Browse by: Latest US Patents, China's latest patents, Technical Efficacy Thesaurus, Application Domain, Technology Topic, Popular Technical Reports.
© 2025 PatSnap. All rights reserved.Legal|Privacy policy|Modern Slavery Act Transparency Statement|Sitemap|About US| Contact US: help@patsnap.com