A new type of nylon material, its preparation method and its application in 3D printing
A new type of nylon technology, applied in the field of nylon materials, can solve the problems of nylon molecular structure and find solutions, so as to improve the mechanical properties and solve the effect of easy warping
- Summary
- Abstract
- Description
- Claims
- Application Information
AI Technical Summary
Problems solved by technology
Method used
Image
Examples
Embodiment 1
[0042] 1) Disperse 1mol of methyl methacrylate and 1mol of allylamine in 5000ml of methanol and water in a mixed solvent with a volume ratio of 1:1, add 0.01mol of EGDMA, 0.2mol of PVP K90, and 0.01mol of AIBN to the system in sequence, and then React at 60°C for 25 hours in a nitrogen environment, dehydrate and dry to obtain polymer a, and the number average molecular weight of polymer a is 105103Da as detected by GPC;
[0043] 2) Disperse 2.5 mol of polyamide 12 (1000) in 5000 mL of N-methylpyrrolidone, react with 5 mol of thionyl chloride and 0.05 mol of polymer a at 5°C under a nitrogen atmosphere for 5 hours, pour the product into hot water, and collect The precipitated product is polymer b, and the number average molecular weight of polymer b detected by GPC is 156890Da;
[0044] 3) Reflux 0.05 mol of polymer b and 8 mol of sodium hydroxide in methanol solvent at 80°C for 18 hours, remove the solvent by rotary evaporation, wash the obtained powder with sodium bicarbonate...
Embodiment 2
[0047] 1) Disperse 3 mol of ethyl acrylate and 1 mol of diallylamine in 20000 ml of methanol and water in a mixed solvent with a volume ratio of 1:1, add 0.03 mol of EGDMA, 0.3 mol of PVP K90, and 0.03 mol of AIBN to the system in turn, at 60 ℃, under nitrogen environment for 30 hours, dehydration and drying to obtain polymer a, the number average molecular weight of polymer a detected by GPC is 120965Da;
[0048] 2) Disperse 5 mol of polyamide 11 (1000) in 20,000 mL of N-methylpyrrolidone, react with 8 mol of oxalyl chloride and 0.05 mol of polymer a at 20°C under a nitrogen atmosphere for 0.5 h, pour the product into hot water, and collect the precipitate The product is polymer b, and the number average molecular weight of polymer b detected by GPC is 278539Da;
[0049] 3) Reflux 0.05mol of polymer b and 5mol of sodium hydroxide in methanol solvent at 60°C for 25 hours, remove the solvent by rotary evaporation, wash the obtained powder with sodium bicarbonate, dilute hydroch...
Embodiment 3
[0052] 1) Disperse 5 mol of ethyl acrylate and 1 mol of crotonic acid in 20000 ml of ethanol and water in a mixed solvent with a volume ratio of 1:1, add 0.02 mol of EGDMA, 0.5 mol of PVP K90, 0.1 mol of AIBN to the system in turn, at 70 ℃, Reaction under nitrogen environment for 20h, dehydration and drying to obtain polymer a, the number average molecular weight of polymer a detected by GPC is 113296Da;
[0053] 2) Disperse 4 mol of polyamide 11 (1000) in 20,000 mL of N-methylpyrrolidone, react with 8 mol of oxalyl chloride and 0.05 mol of polymer a at 10°C under a nitrogen atmosphere for 4 hours, pour the product into hot water, and collect the precipitated product That is, polymer b, the number average molecular weight of polymer b detected by GPC is 164008Da;
[0054] 3) Reflux 0.05mol polymer b and 10mol sodium hydroxide in methanol solvent at 75°C for 18h, remove the solvent by rotary evaporation, wash the obtained powder with sodium bicarbonate, dilute hydrochloric acid...
PUM
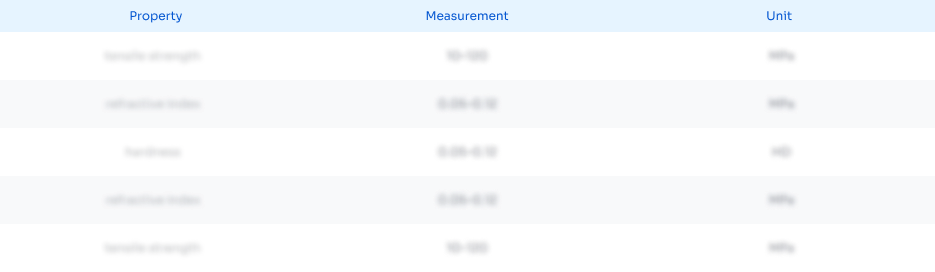
Abstract
Description
Claims
Application Information

- R&D
- Intellectual Property
- Life Sciences
- Materials
- Tech Scout
- Unparalleled Data Quality
- Higher Quality Content
- 60% Fewer Hallucinations
Browse by: Latest US Patents, China's latest patents, Technical Efficacy Thesaurus, Application Domain, Technology Topic, Popular Technical Reports.
© 2025 PatSnap. All rights reserved.Legal|Privacy policy|Modern Slavery Act Transparency Statement|Sitemap|About US| Contact US: help@patsnap.com