Heat-resistant high-temperature-resistant PVC electric power pipe and preparation method thereof
A power tube and high temperature resistance technology, applied in the field of power tubes, can solve problems such as poor stability, and achieve the effects of good heat resistance, increased mechanical properties, good heat resistance and mechanical properties
- Summary
- Abstract
- Description
- Claims
- Application Information
AI Technical Summary
Problems solved by technology
Method used
Examples
Embodiment 1
[0027] Preparation of modified montmorillonite
[0028] S1: Stir and disperse montmorillonite in deionized water at a solid-to-liquid ratio of 3g / L. After ultrasonic dispersion for 30 minutes, add p-phenylenediamine and ammonia water under nitrogen protection conditions. Montmorillonite, p-phenylenediamine, The mass ratio of ammonia water is 1:5:5, stir and react for 4 hours, then raise the temperature to 80°C and keep the temperature for 4 hours, filter, wash the filter cake with hot water and absolute ethanol, dry it and ultrasonicate according to the solid-liquid ratio of 2g / L Dispersed in toluene to obtain a suspension solution;
[0029] S2: Dissolve di-n-butyltin maleate 10 times the mass of montmorillonite in toluene, the solid-to-liquid ratio of di-n-butyltin maleate and toluene is 1:12g / ml, heat to 120°C and ultrasonically until the solution is completely dissolved , add the suspension, in a nitrogen atmosphere, raise the temperature to 100°C and keep it warm for 12h....
Embodiment 2
[0037] The preparation of modified montmorillonite is the same as that of Example 1.
[0038] Preparation of composite modified filler
[0039] Weigh 50 parts by weight of deionized water, 10 parts by weight of α-methylstyrene, 3 parts of acrylonitrile, 0.01 part of tert-dodecylmercaptan, 0.1 part of cumene hydroperoxide, and 1.4 parts of rosin acid soap and stir and mix To obtain the monomer mixed solution, add 100 parts by weight of deionized water, 0.3 parts by weight of glucose, 0.15 parts by weight of sodium pyrophosphate, 0.4 parts by weight of fatty acid potassium salt and 0.0003 parts by weight of ferrous sulfate solution in the reactor, and stir until the solid is completely After dissolving, add 3 parts by weight of potassium abietate, 0.25 parts by weight of potassium hydroxide and 45 parts by weight of polybutadiene latex, then pass into nitrogen, add 2 parts by weight of modified montmorillonite under nitrogen atmosphere, after stirring and dispersing, Add 8 part...
Embodiment 3
[0044] The preparation of modified montmorillonite is the same as that of Example 1.
[0045] Preparation of composite modified filler
[0046] Weigh 75 parts by weight of deionized water, 20 parts by weight of α-methylstyrene, 6 parts of acrylonitrile, 0.02 part of tert-dodecylmercaptan, 0.2 part of cumene hydroperoxide, and 1.5 parts of rosin acid soap and stir and mix To obtain the monomer mixed solution, add 125 parts by weight of deionized water, 0.18 parts by weight of glucose, 0.12 parts by weight of sodium pyrophosphate, 0.25 parts by weight of fatty acid potassium salt and 0.00015 parts by weight of ferrous sulfate solution in the reactor, and stir until the solid is completely After dissolving, add 1.8 parts by weight of potassium abietate, 0.15 parts by weight of potassium hydroxide and 30 parts by weight of polybutadiene latex, then pass into nitrogen, add 3 parts by weight of modified montmorillonite under nitrogen atmosphere, after stirring and dispersing, Add 1...
PUM
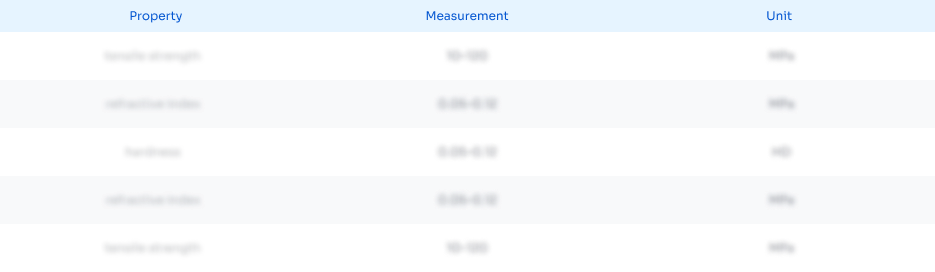
Abstract
Description
Claims
Application Information

- Generate Ideas
- Intellectual Property
- Life Sciences
- Materials
- Tech Scout
- Unparalleled Data Quality
- Higher Quality Content
- 60% Fewer Hallucinations
Browse by: Latest US Patents, China's latest patents, Technical Efficacy Thesaurus, Application Domain, Technology Topic, Popular Technical Reports.
© 2025 PatSnap. All rights reserved.Legal|Privacy policy|Modern Slavery Act Transparency Statement|Sitemap|About US| Contact US: help@patsnap.com