Synthesis of carbon-bound lithium-ion conductor-carbon composite anode materials with carbon fiber structure
A negative electrode material, lithium ion technology, applied in the field of preparation of lithium ion conductor-carbon composite negative electrode materials, can solve the problems of graphite sheet peeling, shortened battery cycle life, poor conductivity, etc.
- Summary
- Abstract
- Description
- Claims
- Application Information
AI Technical Summary
Problems solved by technology
Method used
Image
Examples
Embodiment 1
[0047] As a comparison, in this example, the pure mesocarbon microsphere material was used to prepare a half-cell for testing.
[0048] Battery manufacturing process: Weigh 0.8000g of mesophase carbon microspheres (N 7 ), adding 0.1003g of conductive carbon black and
[0049] 3.3333g of NMP solution containing 3.0% PVDF to make N 7 The mass ratio of conductive carbon black to PVDF is 8:1:1, and the slurry is obtained by ball milling for 30 minutes. The slurry is coated on a copper foil to form a pole piece with a thickness of 90 μm. It is placed in an oven with a nitrogen atmosphere at 120 ° C. Baking for 3 hours, make the pole piece into a half battery in the glove box, first weigh the small disc and put it in the positive electrode shell, then put the separator, 60 μL electrolyte, metal lithium sheet, gasket, shrapnel and negative electrode shell in sequence, and put it in the hydraulic press The upper hydraulic package is a button battery.
[0050] Battery test process: ...
Embodiment 2
[0053] This embodiment is a kind of carbon-bound ZrO with carbon fiber structure prepared by phenolic resin 2 / MgO-carbon composite negative electrode material, and made it into a button battery for measurement.
[0054] Material production process:
[0055] (1) Weigh 1324.00g of absolute ethanol, add 25.91g of ZrO 2 , 16.94g of MgO and 385.65g of mesophase carbon microspheres (average particle size 20 μm), so that the metal oxide / carbon mass ratio is 1:9, then add 64.27g of ethanol solution containing 20wt% phenolic resin, phenolic resin accounted for ZrO 2 .
[0056] (2) Spray drying at 100° C. to obtain solid powder.
[0057] (3) Take 5.0012g of the above-mentioned solid powder in a tube furnace, 2 Next, fired at 800 °C for 5 h to obtain carbon-bound ZrO with carbon fiber structure prepared by phenolic resin 2 / MgO-carbon composite anode material.
[0058] Battery manufacturing process: Weigh the above-mentioned composite negative electrode material, conductive carbo...
Embodiment 3
[0062] This embodiment is a kind of carbon bound ZrO prepared from polyacrylonitrile with carbon fiber structure 2 / CaO-carbon composite negative electrode material, and made it into a button battery for measurement.
[0063] Material production process:
[0064] (1) Weigh 100.00g of water, add 21.54g of ZrO 2 and 20.01 g of CaCO 3 , make the molar ratio of Zr:Ca be 1:2, add the polyvinyl alcohol (PEG) of 12.52g, make PEG account for ZrO 2 and CaCO 3 30% of the total in the ball mill
[0065] 250r / min ball mill for 10h, discharge, add 120.0mL water to rinse, spray dry at 120°C to obtain white powder. Take 25.00 g of the white powder and put it in an air-atmosphere tube furnace for firing at 1000°C for 7 hours, and the fired sample is pulverized through an 80-mesh sieve.
[0066] (2) Weigh 6.96g of the above-mentioned fired sample, add 10.0mL NMP and 27.84g of carbon (N7) to make the inorganic / carbon mass ratio 2:8, then add 34.8g of 5wt.% polypropylene Nitrile NMP solut...
PUM
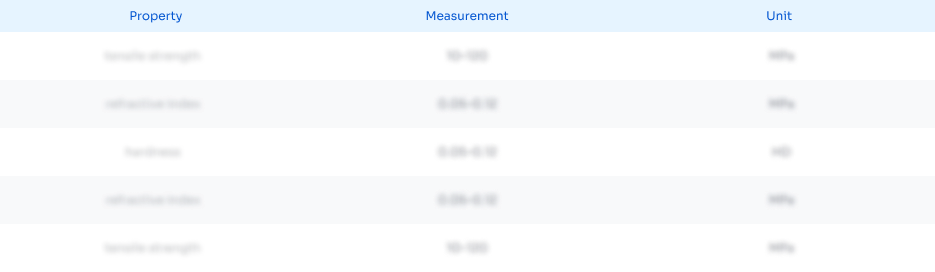
Abstract
Description
Claims
Application Information

- R&D Engineer
- R&D Manager
- IP Professional
- Industry Leading Data Capabilities
- Powerful AI technology
- Patent DNA Extraction
Browse by: Latest US Patents, China's latest patents, Technical Efficacy Thesaurus, Application Domain, Technology Topic, Popular Technical Reports.
© 2024 PatSnap. All rights reserved.Legal|Privacy policy|Modern Slavery Act Transparency Statement|Sitemap|About US| Contact US: help@patsnap.com