Waste incineration flue gas cooling and quenching integrated device
A technology for incinerating flue gas and waste, which is applied in the field of waste incineration flue gas cooling and quenching integrated devices, which can solve the problems of complex phase composition, heavy weight of cooling and cooling devices, and reduced reliability, so as to improve the heat transfer effect , reduce the weight of the equipment, and improve the reliability
- Summary
- Abstract
- Description
- Claims
- Application Information
AI Technical Summary
Problems solved by technology
Method used
Image
Examples
Embodiment Construction
[0023] The specific implementation manner of the present invention will be described below in conjunction with the accompanying drawings.
[0024] Such as figure 1 As shown, the waste incineration flue gas cooling and quenching integrated device of this embodiment includes a first furnace body 1, a high-temperature incineration flue gas inlet 9 is provided at the bottom, and a connecting hole is provided in the middle of the first furnace body 1. The second furnace body 2 with a reduced diameter has a cooled low-temperature incineration flue gas outlet 10 at the top, a furnace body inlet 21 at the bottom, and a diversion partition in the first furnace body 1 below the furnace body inlet 21 6;
[0025] It also includes a close-packed coil pipe 3, which is located between the inner wall of the first furnace body 1 and the outer wall of the second furnace body 2. The first coil 31 is arranged, and the inner ring of the first coil 31 is successively provided with the second coil...
PUM
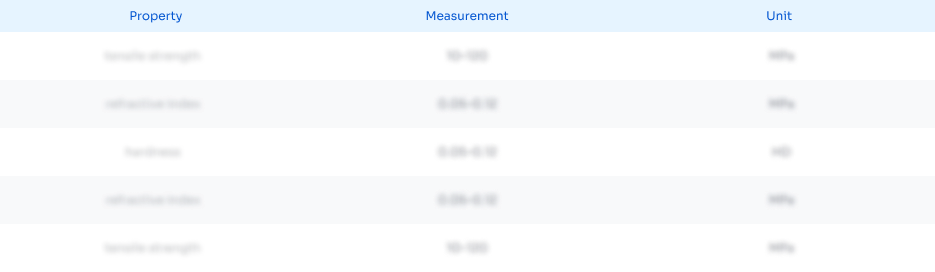
Abstract
Description
Claims
Application Information

- R&D
- Intellectual Property
- Life Sciences
- Materials
- Tech Scout
- Unparalleled Data Quality
- Higher Quality Content
- 60% Fewer Hallucinations
Browse by: Latest US Patents, China's latest patents, Technical Efficacy Thesaurus, Application Domain, Technology Topic, Popular Technical Reports.
© 2025 PatSnap. All rights reserved.Legal|Privacy policy|Modern Slavery Act Transparency Statement|Sitemap|About US| Contact US: help@patsnap.com