Ultrathin friction plate and preparation method thereof
A friction plate and ultra-thin technology, applied in the field of ultra-thin friction plate and its preparation, to achieve the effect of low degree of eccentricity of the center of gravity, high degree of integration, and reduced size
- Summary
- Abstract
- Description
- Claims
- Application Information
AI Technical Summary
Problems solved by technology
Method used
Image
Examples
Embodiment 1
[0051] An ultra-thin friction sheet prepared by the following method:
[0052] Surface friction layer 001 preparation:
[0053] First, 15 parts by weight of phenolic resin, 12 parts by weight of rubber powder, 10 parts by weight of fiber material, 8 parts by weight of wollastonite, 8 parts by weight of barium sulfate, 10 parts by weight of kaolin, and 4 parts by weight of friction powder , 6 parts by weight of aluminum oxide, 6 parts by weight of silicon carbide, 2 parts by weight of ceramic beads, 2 parts by weight of calcium carbonate, 5 parts by weight of calcium hydroxide and 1 part by weight of accelerator mixed mixture , and then perform cold pressing to form the surface friction layer 001.
[0054] Specifically, 10 parts by weight of the fiber material is composed of 7 parts by weight of mineral fiber, 2 parts by weight of aramid fiber and 1 part by weight of acrylic fiber.
[0055] Preparation of reinforced core board 002:
[0056] Spray the surface of the carbon fi...
Embodiment 2
[0062] An ultra-thin friction sheet prepared by the following method:
[0063] Surface friction layer 001 preparation:
[0064] First, 25 parts by weight of phenolic resin, 7 parts by weight of rubber powder, 20 parts by weight of fiber material, 13 parts by weight of wollastonite, 13 parts by weight of barium sulfate, 5 parts by weight of kaolin, and 7 parts by weight of friction powder , 3 parts by weight of aluminum oxide, 3 parts by weight of silicon carbide, 5 parts by weight of ceramic beads, 5 parts by weight of calcium carbonate, 2 parts by weight of calcium hydroxide and 3 parts by weight of accelerator mixed mixture , and then perform cold pressing to form the surface friction layer 001.
[0065] Specifically, 20 parts by weight of the fiber material is composed of 15 parts by weight of mineral fiber, 3 parts by weight of aramid fiber and 5 parts by weight of acrylic fiber.
[0066] Preparation of reinforced core board 002:
[0067] Spray the surface of the carbon...
Embodiment 3
[0073] An ultra-thin friction sheet prepared by the following method:
[0074] Surface friction layer 001 preparation:
[0075] First, 20 parts by weight of phenolic resin, 11 parts by weight of rubber powder, 15 parts by weight of fiber material, 10 parts by weight of wollastonite, 11 parts by weight of barium sulfate, 8 parts by weight of kaolin, and 5 parts by weight of friction powder , the aluminum oxide of 5 parts by weight, the silicon carbide of 5 parts by weight, the ceramic bead of 4 parts by weight, the calcium carbonate of 4 parts by weight, the calcium hydroxide of 4 parts by weight and the accelerator mixed of 1 part by weight , and then perform cold pressing to form the surface friction layer 001.
[0076] Specifically, 15 parts by weight of the fiber material is composed of 10 parts by weight of mineral fiber, 3 parts by weight of aramid fiber and 2 parts by weight of acrylic fiber.
[0077] Preparation of reinforced core board 002:
[0078] Spray the surfac...
PUM
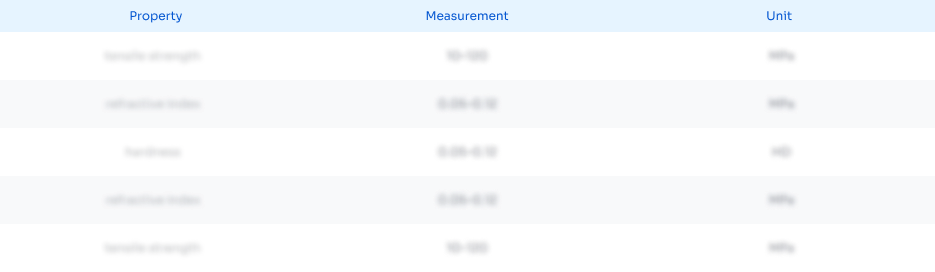
Abstract
Description
Claims
Application Information

- R&D
- Intellectual Property
- Life Sciences
- Materials
- Tech Scout
- Unparalleled Data Quality
- Higher Quality Content
- 60% Fewer Hallucinations
Browse by: Latest US Patents, China's latest patents, Technical Efficacy Thesaurus, Application Domain, Technology Topic, Popular Technical Reports.
© 2025 PatSnap. All rights reserved.Legal|Privacy policy|Modern Slavery Act Transparency Statement|Sitemap|About US| Contact US: help@patsnap.com