Construction basal layer material and construction method
A base layer and civil engineering technology, applied in the direction of roads, roads, buildings, etc., can solve the problems of good anti-seepage performance and high compressive strength, and achieve the effect of simple preparation process, less usage and excellent compressive strength
- Summary
- Abstract
- Description
- Claims
- Application Information
AI Technical Summary
Problems solved by technology
Method used
Image
Examples
Embodiment 1
[0019] (1) Prepare the following raw materials by weight percentage: 92% alkali slag, 6% calcium silicate slag and 2% composite additive; the composite additive is composed of the following components by weight percentage: 50% sodium fluorosilicate, 25% sulfuric acid Sodium and triethanolamine 25%;
[0020] (2) After mixing the product obtained in step (1), stir and mix evenly to obtain the product.
Embodiment 2
[0022] (1) Prepare the following raw materials by weight percentage: 94% alkali slag, 5% silicon-calcium slag and 1% composite additive; the composite additive is composed of the following components by weight percentage: 70% sodium fluorosilicate, 25% sulfuric acid Sodium and triethanolamine 5%;
[0023] (2) After mixing the product obtained in step (1), stir and mix evenly to obtain the product.
Embodiment 3
[0025] (1) Prepare the following raw materials by weight percentage: 93% alkali slag, 5% silicon-calcium slag and 2% composite additive; the composite additive is composed of the following components by weight percentage: 60% sodium fluorosilicate, 25% sulfuric acid Sodium and triethanolamine 15%;
[0026] (2) After mixing the product obtained in step (1), stir and mix evenly to obtain the product.
PUM
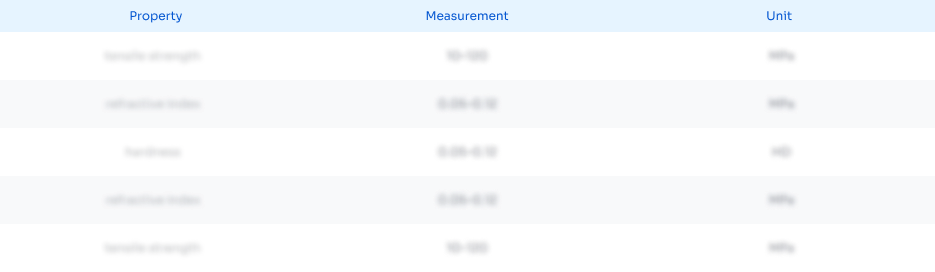
Abstract
Description
Claims
Application Information

- Generate Ideas
- Intellectual Property
- Life Sciences
- Materials
- Tech Scout
- Unparalleled Data Quality
- Higher Quality Content
- 60% Fewer Hallucinations
Browse by: Latest US Patents, China's latest patents, Technical Efficacy Thesaurus, Application Domain, Technology Topic, Popular Technical Reports.
© 2025 PatSnap. All rights reserved.Legal|Privacy policy|Modern Slavery Act Transparency Statement|Sitemap|About US| Contact US: help@patsnap.com