Vacuum spraying treatment technology used for aluminum profile machining
A technology of aluminum profile processing and vacuum spraying, which is applied in the field of aluminum profile processing, can solve problems such as low bonding strength, affecting the service life of the coating, and metal shedding of the coating, so as to improve the bonding firmness, improve mechanical properties, reduce produces a quantitative effect
- Summary
- Abstract
- Description
- Claims
- Application Information
AI Technical Summary
Problems solved by technology
Method used
Examples
Embodiment 1
[0022] Preparation of cleaning solution: measure 45L deionized water, 5kg glycerin, 1kg betaine, 2kg polyoxyethylene ether, 5kg hydrochloric acid, 7kg sodium chloride, 5kg alumina and 3kg phosphoric acid for use;
[0023] Surface treatment of aluminum profiles: use cleaning solution to remove the grease and oxide film layer on the surface of aluminum profiles, put the aluminum alloy in the cleaning solution for degreasing treatment, use ultrasonic auxiliary cleaning during the cleaning process, the ultrasonic power is 200W, and the cleaning time is 15 minutes, and then Rinse and wash with deionized water, and then blow dry the aluminum profile with hot air at 45°C after rinsing.
[0024] Install the zinc sheet inside the vacuum chamber and adjust the pressure of the vacuum chamber to 3×10 -5 Pa, the zinc sheet is heated by electric heating, the electric heating current is 65A, the zinc sheet reaches the melting point, melts and evaporates into gaseous zinc atoms, the rotation ...
Embodiment 2
[0029] Preparation of cleaning solution: measure 60L deionized water, 7kg glycerin, 3kg betaine, 5kg polyoxyethylene ether, 10kg hydrochloric acid, 12kg sodium chloride, 10kg alumina and 5kg phosphoric acid for use;
[0030] Surface treatment of aluminum profiles: Use cleaning solution to remove the grease and oxide film layer on the surface of aluminum profiles, put the aluminum alloy in the cleaning solution for degreasing treatment, use ultrasonic assisted cleaning during the cleaning process, the ultrasonic power is 300W, and the cleaning time is 20min, and then Rinse and wash with deionized water, and then blow dry the aluminum profile with hot air at 55°C after rinsing.
[0031] Install the copper sheet inside the vacuum chamber and adjust the pressure of the vacuum chamber to 4×10 -5 Pa, the copper sheet is heated by electric heating, the electric heating current is 80A, the copper sheet reaches the melting point, melts and evaporates into gaseous copper atoms, the rota...
Embodiment 3
[0036] Preparation of cleaning solution: Measure 50L deionized water, 6kg glycerin, 2kg betaine, 4kg polyoxyethylene ether, 7kg hydrochloric acid, 8kg sodium chloride, 6kg alumina and 4kg phosphoric acid for use;
[0037] Surface treatment of aluminum profiles: Use cleaning solution to remove the grease and oxide film layer on the surface of aluminum profiles, put the aluminum alloy in the cleaning solution for degreasing treatment, use ultrasonic auxiliary cleaning during the cleaning process, the ultrasonic power is 220W, and the cleaning time is 5-20min , and then rinse and wash with deionized water, and then blow dry the aluminum profile with hot air at 47°C after rinsing.
[0038] Install the chromium sheet inside the vacuum chamber and adjust the pressure of the vacuum chamber to 5×10 -5 Pa, the chromium sheet is heated by electric heating, the electric heating current is 70A, the chromium sheet reaches the melting point, melts and evaporates into gaseous chromium atoms,...
PUM
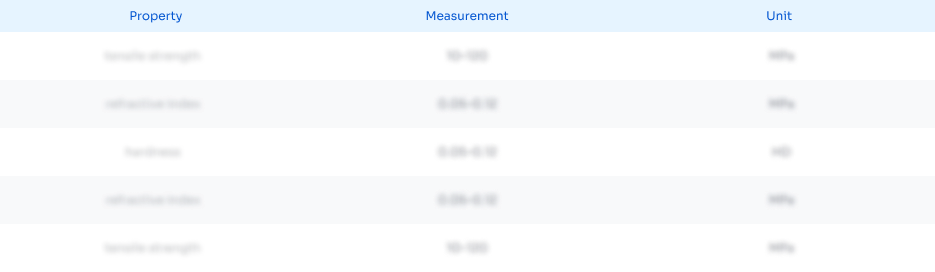
Abstract
Description
Claims
Application Information

- R&D
- Intellectual Property
- Life Sciences
- Materials
- Tech Scout
- Unparalleled Data Quality
- Higher Quality Content
- 60% Fewer Hallucinations
Browse by: Latest US Patents, China's latest patents, Technical Efficacy Thesaurus, Application Domain, Technology Topic, Popular Technical Reports.
© 2025 PatSnap. All rights reserved.Legal|Privacy policy|Modern Slavery Act Transparency Statement|Sitemap|About US| Contact US: help@patsnap.com