Method for preparing benzhydrol by hydrogenation of benzophenone
A technology of benzophenone and benzphenyl alcohol, which is applied in the field of hydrogenation of benzophenone to produce benzphenyl alcohol, can solve the problems of unfavorable large-scale industrial production separation, difficult industrial application, expensive catalyst, etc., and achieve easy large-scale industrialization Effects on production, sintering inhibition, excellent conversion and selectivity
- Summary
- Abstract
- Description
- Claims
- Application Information
AI Technical Summary
Problems solved by technology
Method used
Examples
Embodiment 1
[0029] Mix 4.3 g of copper nitrate, concentrated ammonia water, and deionized water at room temperature to prepare a mixture with a pH of 9.5 to 12.5, add 5.75 g of powdered aluminum oxide to it, and stir for 12 hours at room temperature. The temperature rises to 120°C, and the pH value of the mixed solution is monitored in real time until it drops to 6-7. Filter and wash with deionized water. The obtained solid sample was dried in an oven at 100°C for 6 hours, and then transferred to a muffle furnace for calcination at 650°C for 3 hours to obtain a catalyst Cu / Al 2 O 3 .
[0030] Take 0.1g of the above catalyst and place it in a connected high-temperature reduction furnace to reduce the catalyst. The reduction temperature is 350℃, the reduction time is 1h, the reduction pressure is 0.3MPa, the reducing gas is hydrogen, and the gas space velocity is 3000h. -1 . After the reduction, the temperature was lowered to room temperature and switched to nitrogen. Under the protection of ...
Embodiment 2
[0032] Mix 4.3 g of copper nitrate, concentrated ammonia water, and deionized water at room temperature to prepare a mixture with a pH of 9.5 to 12.5, add 5.75 powdered aluminum oxide to it, and stir for 12 hours at room temperature. The temperature rises to 120°C, and the pH value of the mixed solution is monitored in real time until it drops to 6-7. Filter and wash with deionized water. The obtained solid sample was dried in an oven at 100°C for 6 hours, and then transferred to a muffle furnace for calcination at 650°C for 3 hours to obtain a catalyst Cu / Al 2 O 3 .
[0033] Weigh the 2.0 g sample prepared above, immerse it in an equal volume of the aqueous solution containing palladium nitrate for 36 hours, and dry it in an oven at 100°C for 6 hours. Then transfer to a muffle furnace for calcination at 650°C for 6 hours. The component in the obtained catalyst is Cu-Pd / Al 2 O 3 .
[0034] Take 0.1g of the above catalyst and place it in a connected high-temperature reduction fur...
Embodiment 3
[0036] Mix 4.3 g of copper nitrate, concentrated ammonia water, and deionized water at room temperature to prepare a mixture with a pH of 9.5 to 12.5, add 5.75 g of powdered aluminum oxide to it, and stir for 12 hours at room temperature. The temperature rises to 120°C, and the pH value of the mixed solution is monitored in real time until it drops to 6-7. Filter and wash with deionized water. The obtained solid sample was dried in an oven at 100°C for 6 hours, and then transferred to a muffle furnace for calcination at 650°C for 3 hours to obtain a catalyst Cu / Al 2 O 3 .
[0037] Weigh the 2.0 g sample prepared above, immerse it in an equal volume of an aqueous solution containing magnesium nitrate for 36 hours, and dry it in an oven at 100°C for 6 hours. Then transfer to a muffle furnace for calcination at 650°C for 6 hours. The component in the obtained catalyst is Cu-Mg / Al 2 O 3 .
[0038] Take 0.1g of the above catalyst and place it in a connected high-temperature reduction...
PUM
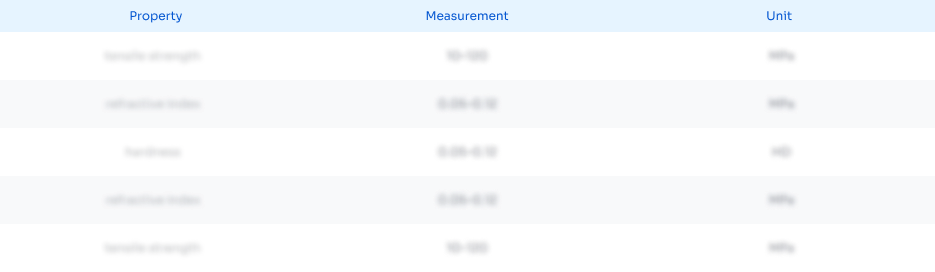
Abstract
Description
Claims
Application Information

- Generate Ideas
- Intellectual Property
- Life Sciences
- Materials
- Tech Scout
- Unparalleled Data Quality
- Higher Quality Content
- 60% Fewer Hallucinations
Browse by: Latest US Patents, China's latest patents, Technical Efficacy Thesaurus, Application Domain, Technology Topic, Popular Technical Reports.
© 2025 PatSnap. All rights reserved.Legal|Privacy policy|Modern Slavery Act Transparency Statement|Sitemap|About US| Contact US: help@patsnap.com