A method for controlling the microstructure and properties of the working layer of a centrifugal roll
A control method and technology of microstructure and performance, applied in the field of steel rolling manufacturing, can solve the problems of long production cycle, high cost, long equipment occupation time, etc., and achieve the effect of long production period, high cost and long equipment occupation time.
- Summary
- Abstract
- Description
- Claims
- Application Information
AI Technical Summary
Problems solved by technology
Method used
Examples
Embodiment 1
[0035] A work roll for hot continuous rolling finish rolling, the diameter of the roll body is 700mm, the working layer is 40mm (radius), and the hardness requirement is HSD77-82. The mass fraction of the component content of the design roll working layer is: C content is 3.1-3.3%, Ni content is 4.0-4.5%, Σ(Cr+Mo+V+W) content is 2.2-2.4%, and the remaining components For Fe and unavoidable impurities.
[0036] The measured solidus of this design composition is about 1140°C, the pearlite range is about 710~630°C, the critical cooling rate is required to be 0.01°C / s; the bainite temperature range is 480~380°C, and the "nose tip" temperature is about 410°C .
[0037] Sampling before casting to analyze the chemical composition of molten iron meets the requirements.
[0038] After the solidus line of the product is finished filling the core (core filling temperature is 1020°C), it is placed in a well-ventilated pouring pit for cooling after 6 hours. It is measured that the temper...
Embodiment 2
[0043] A work roll for finish rolling of wide and heavy plate mills, the diameter of the roll body is 1200mm, the working layer is 50mm (radius), and the hardness requirement is HSD72-78. The mass fractions of the components in the design roll working layer are: C content 2.9-3.1%, Ni content 4.2-4.6%, Σ(Cr+Mo+V+W) content 2.0-2.3%, and the remaining components For Fe and unavoidable impurities.
[0044] The measured solidus of this design composition is about 1140°C, the pearlite range is about 700~620°C, the critical cooling rate is required to be 0.008°C / s; the bainite temperature range is 460~360°C, and the "nose tip" temperature is about 400°C .
[0045] Sampling before casting to analyze the chemical composition of molten iron meets the requirements.
[0046] After the solidus line of the product finishes filling the core (core filling temperature is 1000°C), place it in a well-ventilated pouring pit for cooling after 12 hours. It is measured that the temperature drops...
PUM
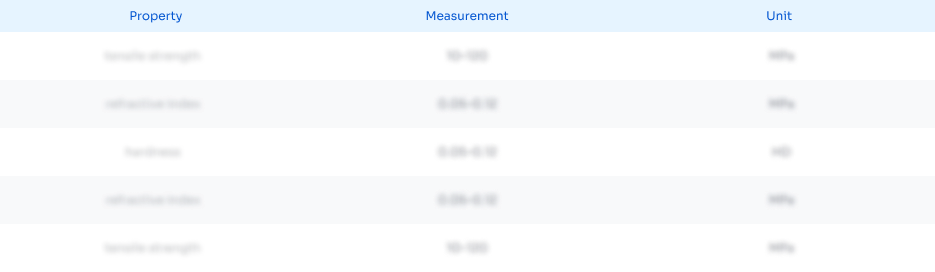
Abstract
Description
Claims
Application Information

- R&D Engineer
- R&D Manager
- IP Professional
- Industry Leading Data Capabilities
- Powerful AI technology
- Patent DNA Extraction
Browse by: Latest US Patents, China's latest patents, Technical Efficacy Thesaurus, Application Domain, Technology Topic, Popular Technical Reports.
© 2024 PatSnap. All rights reserved.Legal|Privacy policy|Modern Slavery Act Transparency Statement|Sitemap|About US| Contact US: help@patsnap.com