Cold extrusion forming technology of brake shoe roller shaft
A molding process and roller shaft technology, applied in the field of machine parts processing, can solve the problems of a large number of cracks on the surface of the product, unable to obtain qualified products, unreasonable process design, etc., and achieve small batch differences, small deviation between samples, and smooth surface. Effect
- Summary
- Abstract
- Description
- Claims
- Application Information
AI Technical Summary
Problems solved by technology
Method used
Examples
Embodiment 1
[0027] Using round steel as raw material, after sawing according to the specifications and sizes, annealing, flat head, shot blasting, phosphorus saponification treatment, cold extrusion shaping, machining, quenching, tempering, shot blasting, cleaning, and grinding machine processing are performed in sequence to obtain finished products. Moving hoof roller shaft.
[0028] The annealing is carried out in an industrial quenching resistance furnace, the annealing temperature is 750-800° C., and the annealing time is 6-7 hours. The annealing temperature is slightly lower than that of the prior art, mainly for cost reduction, and the treatment process has been tested to meet the usage requirements.
[0029] The flat head is carried out according to the conventional process, but it should be noted that the execution standard of the flat head is to strictly ensure the quality consistency among individuals.
[0030] The shot blasting refers to surface shot blasting treatment with ca...
PUM
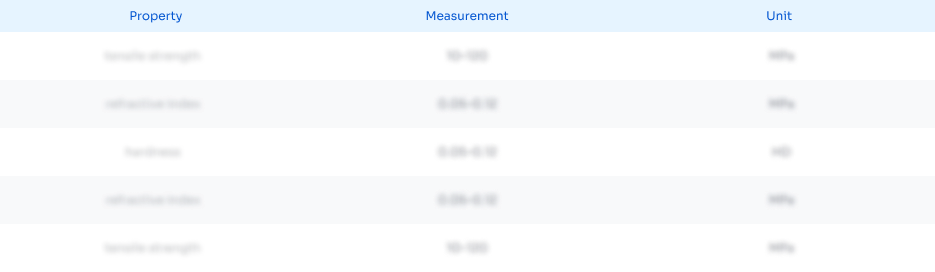
Abstract
Description
Claims
Application Information

- R&D
- Intellectual Property
- Life Sciences
- Materials
- Tech Scout
- Unparalleled Data Quality
- Higher Quality Content
- 60% Fewer Hallucinations
Browse by: Latest US Patents, China's latest patents, Technical Efficacy Thesaurus, Application Domain, Technology Topic, Popular Technical Reports.
© 2025 PatSnap. All rights reserved.Legal|Privacy policy|Modern Slavery Act Transparency Statement|Sitemap|About US| Contact US: help@patsnap.com