Silane-terminated polyether sealing gum and preparation method thereof
A technology of silane-capped polyether and capped polyether, which is applied in the field of sealants, can solve problems such as poor heat resistance, low strength, and unstable structure, and achieve the effects of improving mechanical properties, excellent product performance, and reducing production costs
- Summary
- Abstract
- Description
- Claims
- Application Information
AI Technical Summary
Problems solved by technology
Method used
Examples
Embodiment 1
[0027] Preparation of short-chain silane-terminated polyether polyols: (1) Allyl alcohol polyoxyethylene ether and toluene diisocyanate with a number-average molecular weight of 500 g / mol were added to the reaction flask at a molar ratio of 2:1, and heated to 60 ℃, and reacted for 3 hours under the protection of nitrogen to form a carbon-carbon double bond-terminated prepolymer W1: add the carbon-carbon double-bond-terminated prepolymer W1 and hydrogen-containing trimethoxysilane in a molar ratio of 1:1 to Add 60ppm chloroplatinic acid catalyst into the reaction bottle, heat to 90°C, and react for 6h under the protection of nitrogen to prepare short-chain silane-terminated polyether polyol.
[0028] Preparation of long-chain silane-terminated polyether polyols: (1) Allyl alcohol polyoxypropylene ether and toluene diisocyanate with a number-average molecular weight of 6000 g / mol were added to the reaction flask at a molar ratio of 2:1, and heated to 90 ℃, and reacted for 2 hour...
Embodiment 2
[0031] Preparation of short-chain silane-terminated polyether polyols: (1) Allyl alcohol polyoxypropylene ether and isophorone diisocyanate with a number average molecular weight of 1000 g / mol were added to the reaction flask at a molar ratio of 2:1, Heat to 90°C and react for 2 hours under the protection of nitrogen to form a carbon-carbon double bond-terminated prepolymer W1: the carbon-carbon double-bond-terminated prepolymer W1 and hydrogen-containing trimethoxysilane are in a molar ratio of 1: 2 into a reaction flask, and 30 ppm chloroplatinic acid catalyst was added, heated to 120° C., and reacted for 3 hours under the protection of nitrogen, and reacted to prepare a short-chain silane-terminated polyether polyol.
[0032] Preparation of long-chain silane-terminated polyether polyols: (1) Allyl alcohol polyoxyethylene ether with a number average molecular weight of 4000 g / mol and isophorone diisocyanate were added to the reaction flask at a molar ratio of 2:1, Heat to 90...
Embodiment 3
[0035] Preparation of short-chain silane-terminated polyether polyols: (1) Allyl alcohol polyoxypropylene ether with a number average molecular weight of 750 g / mol and diphenylmethane diisocyanate were added to the reaction flask at a molar ratio of 1.5:1, Heat to 75°C and react for 2.5 hours under the protection of nitrogen to form a carbon-carbon double bond-terminated prepolymer W1: the carbon-carbon double-bond-terminated prepolymer W1 and hydrogen-containing trimethoxysilane are in a molar ratio of 1 : 1.5 was added to the reaction bottle, and 45ppm chloroplatinic acid catalyst was added, heated to 105°C, and reacted for 4.5h under the protection of nitrogen to prepare short-chain silane-terminated polyether polyol.
[0036] Preparation of long-chain silane-terminated polyether polyol: (1) Prenol polyoxyethylene ether with a number average molecular weight of 5000 g / mol and diphenylmethane diisocyanate are added to the reaction flask at a molar ratio of 1.5:1 , heated to ...
PUM
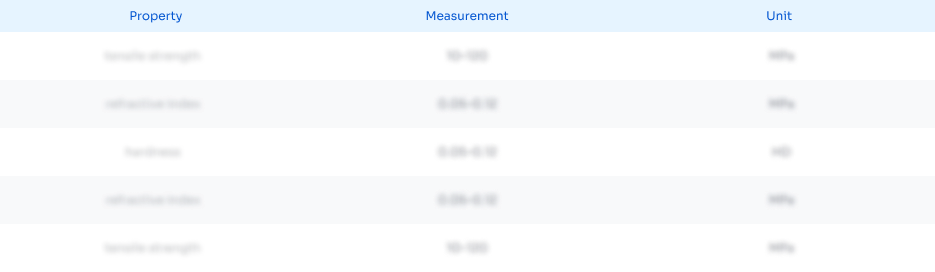
Abstract
Description
Claims
Application Information

- R&D Engineer
- R&D Manager
- IP Professional
- Industry Leading Data Capabilities
- Powerful AI technology
- Patent DNA Extraction
Browse by: Latest US Patents, China's latest patents, Technical Efficacy Thesaurus, Application Domain, Technology Topic, Popular Technical Reports.
© 2024 PatSnap. All rights reserved.Legal|Privacy policy|Modern Slavery Act Transparency Statement|Sitemap|About US| Contact US: help@patsnap.com