Manufacture technology for anti-corrosion, low-cost, refined and environment-friendly stainless steel wire
A technology of stainless steel wire and manufacturing process, which is applied in the field of manufacturing process of corrosion-resistant, low-cost, refined and environmentally friendly stainless steel wire. It can solve the problems affecting the production and sales of stainless steel, the fluctuation of nickel price is particularly large, and the reduction of production efficiency, so as to achieve the reduction of Ni content. , composition uniformity, enhanced probability and the effect of the speed of vortex water flow
- Summary
- Abstract
- Description
- Claims
- Application Information
AI Technical Summary
Problems solved by technology
Method used
Examples
Embodiment Construction
[0024] The specific implementation of the present invention will be further described below in conjunction with the examples. The following examples are only used to illustrate the technical solution of the present invention more clearly, but not to limit the protection scope of the present invention.
[0025] The present invention is a manufacturing process of corrosion-resistant and low-cost refined environment-friendly stainless steel wire, including the following process steps:
[0026] S1: Using chromium-iron alloy and nickel-iron alloy ingredients;
[0027] S2: Put the ingredients into the electric arc furnace in order to heat and melt, and detect the content of each element, keep warm during the test, adjust the various chemical components according to the test results, and then make slag. When the furnace temperature reaches 1650°C, remove the slag and tap the steel;
[0028] A spiral flow channel with a height lower than the bottom wall of the furnace cavity is set a...
PUM
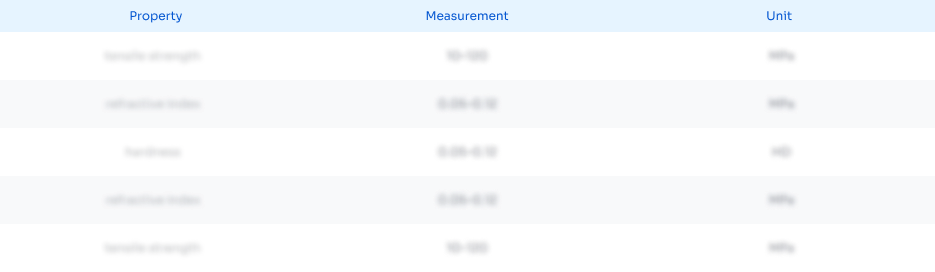
Abstract
Description
Claims
Application Information

- Generate Ideas
- Intellectual Property
- Life Sciences
- Materials
- Tech Scout
- Unparalleled Data Quality
- Higher Quality Content
- 60% Fewer Hallucinations
Browse by: Latest US Patents, China's latest patents, Technical Efficacy Thesaurus, Application Domain, Technology Topic, Popular Technical Reports.
© 2025 PatSnap. All rights reserved.Legal|Privacy policy|Modern Slavery Act Transparency Statement|Sitemap|About US| Contact US: help@patsnap.com