Continuous production method of biquaternary ammonium salt
A technology of a biquaternary ammonium salt and a production method, applied in the field of fine chemicals, can solve the problems of using a large amount of organic solvents, high production cost, long reaction period, etc., and achieves that the reaction end point is easy to define, the reaction speed is increased, and the reaction balance is changed. Effect
- Summary
- Abstract
- Description
- Claims
- Application Information
AI Technical Summary
Problems solved by technology
Method used
Image
Examples
Embodiment 1
[0022] Add the materials into the mixing tank at a constant speed according to the flow rate of dodecyldimethyl tertiary amine 101.2kg / h, 1,3-dichloropropane 56.5kg / h, pure water 57.5kg / h, and start stirring at the same time, after 10min , pump the mixed material into the first-stage static mixer at a constant speed of 220.5kg / h, and control the temperature in the continuous reactor to 118±2°C through the jacket, and the material enters the first-stage continuous reaction at a uniform speed after being mixed by the first-stage static mixer Reaction in the container, after 3.78 hours of reaction, the material flows from the first-stage continuous reactor to the second-stage static mixer. At this time, dodecyl dimethyl tertiary amine is added at a constant speed at a flow rate of 111.8kg / h, and the mixed material is passed through the second-stage static mixer. After being mixed by the static mixer, it enters the two-stage continuous reactor for reaction. After 4.03 hours of reac...
Embodiment 2
[0024] Add materials into the mixing tank at a constant speed according to the flow rate of 101.2kg / h dodecyldimethyl tertiary amine, 64.5kg / h 1,3-dichloropropanol, and 57.5kg / h pure water, and start stirring at the same time, stirring After 10 minutes, pump the mixed material into the first-stage static mixer at a constant speed of 228.5kg / h, and control the temperature in the continuous reactor to 118±2°C through the jacket, and the material enters the first-stage static mixer at a uniform speed after being mixed by the first-stage static mixer. React in the continuous reactor. After 4.02 hours of reaction, the material changes from turbid to clear. The material flows from the first-stage continuous reactor to the second-stage static mixer. At this time, tetradecyldimethyl Tertiary amine, the mixed material is mixed by the secondary static mixer and then enters the secondary continuous reactor for reaction. After 4.12 hours of reaction, the material is pumped into the dilutio...
Embodiment 3
[0026] Add the materials into the mixing tank at a constant speed according to the flow rate of quinoline 66.2kg / h, 1,3-dichloropropanol 69.7kg / h, and pure water 57.5kg / h, and start stirring at the same time. After stirring for 10 minutes, mix the materials with The flow rate of 196.9kg / h is pumped into the first-stage static mixer at a constant speed, and the temperature in the continuous reactor is controlled by the jacket to be 118±2°C. After being mixed by the first-stage static mixer, the materials enter the first-stage continuous reactor at a uniform speed for reaction. After 3.85 hours, the material changed from turbidity to clarification, and the material flowed from the first-stage continuous reactor to the second-stage static mixer. At this time, hexadecyldimethyl tertiary amine was added at a constant speed at a flow rate of 152.5kg / h, and the mixed material was passed through two After being mixed by the first-stage static mixer, it enters the second-stage continuou...
PUM
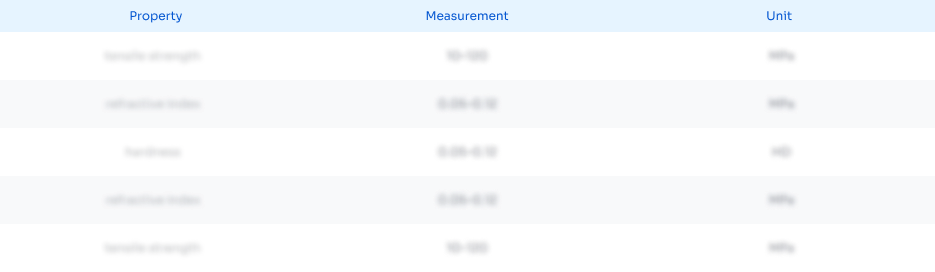
Abstract
Description
Claims
Application Information

- Generate Ideas
- Intellectual Property
- Life Sciences
- Materials
- Tech Scout
- Unparalleled Data Quality
- Higher Quality Content
- 60% Fewer Hallucinations
Browse by: Latest US Patents, China's latest patents, Technical Efficacy Thesaurus, Application Domain, Technology Topic, Popular Technical Reports.
© 2025 PatSnap. All rights reserved.Legal|Privacy policy|Modern Slavery Act Transparency Statement|Sitemap|About US| Contact US: help@patsnap.com