Forging technology for synchronous waste-removing and weight-reduction of forge piece
A technology for removing waste and forgings, applied in the field of forgings processing, can solve the problems of high price, increased cost, increased equipment workload, etc., and achieve the effect of high mechanical strength, uniform structure, and reduced deformation
- Summary
- Abstract
- Description
- Claims
- Application Information
AI Technical Summary
Problems solved by technology
Method used
Image
Examples
Embodiment 1
[0051] see figure 1 , a forging process for removing waste and reducing weight of synchronous forgings, comprising the following steps:
[0052] S1. Blanking: Calculate the size of the forging material according to the drawings, and cut the forging material into blanks through automatic cutting. The weight of the blanking material is 1.02 times the theoretical weight. Through process optimization, on the basis of meeting the premise of blanking, the maximum Save raw materials and reduce forging costs;
[0053] S2. Annealing: Send the billet into the heating furnace and slowly heat it to a temperature of 720°C, and the annealing heating rate is 100°C / h. Uniform and slow annealing treatment can make the structure and composition of the forging material more uniform, improve its plasticity, and facilitate Subsequent forging treatment, after 1.5 hours of heat preservation, quickly transferred to a heating furnace with a temperature of 680 ° C, kept isothermally until the austenit...
Embodiment 2
[0076] see figure 1 , a forging process for removing waste and reducing weight of synchronous forgings, comprising the following steps:
[0077] S1. Blanking: Calculate the size of the forging material according to the drawings, and cut the forging material into blanks through automatic cutting. The weight of the blanking material is 1.04 times the theoretical weight;
[0078] S2. Annealing: Put the billet into the heating furnace and slowly heat it to a temperature of 740°C. The annealing heating rate is 100-150°C / h. After 1.5 hours of heat preservation, it is quickly transferred to a heating furnace with a temperature of 690°C. Until the austenite is completely transformed into lamellar pearlite, it is air-cooled after being released from the furnace;
[0079] S3, descaling: pass the heated billet through the forging blank peeling machine to clean the oxide scale attached to the surface of the red hot billet after heating;
[0080] S4, upsetting: placing the blank on the u...
Embodiment 3
[0095] see figure 1 , a forging process for removing waste and reducing weight of synchronous forgings, comprising the following steps:
[0096] S1. Blanking: Calculate the size of the forging material according to the drawings, and cut the forging material into blanks through automatic cutting. The weight of the blanking material is 1.05 times the theoretical weight;
[0097] S2. Annealing: Put the billet into the heating furnace and slowly heat it to a temperature of 760°C. The annealing heating rate is 150°C / h. After holding the heat for 2 hours, it is quickly transferred to a heating furnace with a temperature of 700°C, and isothermally maintained until it is austenitic. The body is all transformed into lamellar pearlite, and it is air-cooled after being released from the furnace;
[0098] S3, descaling: pass the heated billet through the forging blank peeling machine to clean the oxide scale attached to the surface of the red hot billet after heating;
[0099] S4, upset...
PUM
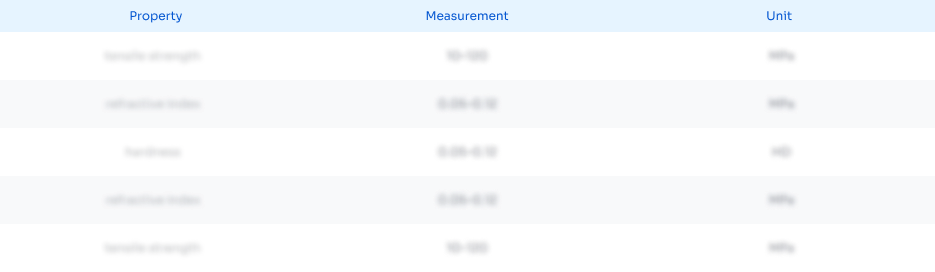
Abstract
Description
Claims
Application Information

- R&D
- Intellectual Property
- Life Sciences
- Materials
- Tech Scout
- Unparalleled Data Quality
- Higher Quality Content
- 60% Fewer Hallucinations
Browse by: Latest US Patents, China's latest patents, Technical Efficacy Thesaurus, Application Domain, Technology Topic, Popular Technical Reports.
© 2025 PatSnap. All rights reserved.Legal|Privacy policy|Modern Slavery Act Transparency Statement|Sitemap|About US| Contact US: help@patsnap.com