Microwave dielectric ceramic with layered structure and preparation method thereof
A technology of microwave dielectric ceramics and layered structure, applied in the field of microwave dielectric ceramics, can solve the problems of large fluctuations in ceramic performance, lower quality factors, and difficulty in meeting stability, and achieve the effect of improving stability and quality factors
- Summary
- Abstract
- Description
- Claims
- Application Information
AI Technical Summary
Problems solved by technology
Method used
Image
Examples
Embodiment 1
[0036] The first embodiment provides a method for preparing a layered microwave dielectric ceramic, such as figure 1 shown, including the following steps:
[0037] S1, the BaTi 4 o 9 and Zn 1.01 Nb 2 o 6 Placed in a ball mill, the BaTi 4 o 9 and the Zn 1.01 Nb 2 o 6 Ball milled into BaTi 4 o 9 Powder and Zn 1.01 Nb 2 o 6 powder to make the BaTi 4 o 9 powder and the Zn 1.01 Nb 2 o 6 The particle size of the powder meets the preset particle size;
[0038] S2, the BaTi 4 o 9 powder and the Zn 1.01 Nb 2 o 6 powder according to BaTi 4 o 9 -Zn 1.01 Nb 2 o 6 The chemical composition is weighed;
[0039] S3, 50% of the BaTi in the S2 step 4 o 9 The powder is placed in the mold, and the first substrate is prepared by dry pressing;
[0040] S4. Place the Zn on the first substrate 1.01 Nb 2 o 6 Powder, the second substrate is prepared by dry pressing;
[0041] S5. Place the remaining 50% of the BaTi in the step S2 on the second substrate 4 o 9 Powder,...
Embodiment 2
[0060] The second embodiment provides a method for preparing a layered microwave dielectric ceramic, such as figure 1 shown, including the following steps:
[0061] S1, the BaTi 4 o 9 and Zn 1.01 Nb 2 o 6 Placed in a ball mill, the BaTi 4 o 9 and the Zn 1.01 Nb 2 o 6 Ball milled into BaTi 4 o 9 Powder and Zn 1.01 Nb 2 o 6 powder to make the BaTi 4 o 9 powder and the Zn 1.01 Nb 2 o 6 The particle size of the powder meets the preset particle size;
[0062] S2, the BaTi 4 o 9 powder and the Zn 1.01 Nb 2 o 6 powder according to BaTi 4 o 9 -Zn 1.01 Nb 2 o 6 The chemical composition is weighed;
[0063] S3, 50% of the BaTi in the S2 step 4 o 9 The powder is placed in the mold, and the first substrate is prepared by dry pressing;
[0064] S4. Place the Zn on the first substrate 1.01 Nb 2 o 6 Powder, the second substrate is prepared by dry pressing;
[0065] S5. Place the remaining 50% of the BaTi in the step S2 on the second substrate 4 o 9 Powd...
Embodiment 3
[0084] This implementation provides a method for preparing microwave dielectric ceramics with a layered structure, such as figure 1 shown, including the following steps:
[0085] S1, the BaTi 4 o 9 and Zn 1.01 Nb 2 o 6 Placed in a ball mill, the BaTi 4 o 9 and the Zn 1.01 Nb 2 o 6 Ball milled into BaTi 4 o 9 Powder and Zn 1.01 Nb 2 o 6 powder to make the BaTi 4 o 9 powder and the Zn 1.01 Nb 2 o 6 The particle size of the powder meets the preset particle size;
[0086] S2, the BaTi 4 o 9 powder and the Zn 1.01 Nb 2 o 6 powder according to BaTi 4 o 9 -Zn 1.01 Nb 2 o 6 The chemical composition is weighed;
[0087] S3, 50% of the BaTi in the S2 step 4 o 9 The powder is placed in the mold, and the first substrate is prepared by dry pressing;
[0088] S4. Place the Zn on the first substrate 1.01 Nb 2 o 6 Powder, the second substrate is prepared by dry pressing;
[0089] S5. Place the remaining 50% of the BaTi in the step S2 on the second substrat...
PUM
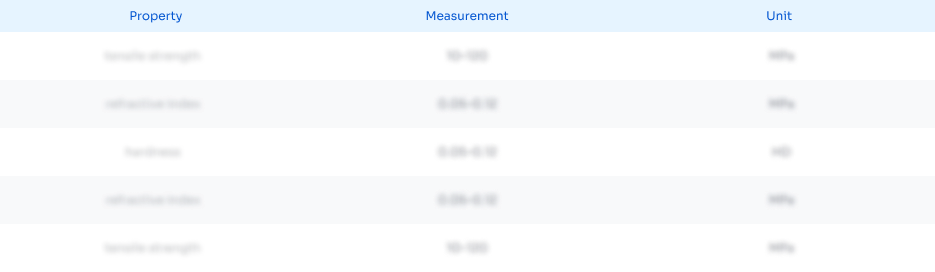
Abstract
Description
Claims
Application Information

- R&D
- Intellectual Property
- Life Sciences
- Materials
- Tech Scout
- Unparalleled Data Quality
- Higher Quality Content
- 60% Fewer Hallucinations
Browse by: Latest US Patents, China's latest patents, Technical Efficacy Thesaurus, Application Domain, Technology Topic, Popular Technical Reports.
© 2025 PatSnap. All rights reserved.Legal|Privacy policy|Modern Slavery Act Transparency Statement|Sitemap|About US| Contact US: help@patsnap.com