Treatment method for reducing emission of harmful substance generated by surface treatment of aluminum product
A technology of surface treatment and harmful substances, which is applied in the field of reducing the discharge of harmful substances produced by the surface treatment of aluminum products. It can solve the problems of environmental hazards, increase the cost and difficulty of sewage treatment, and achieve the improvement of acid and alkali corrosion resistance and comprehensive improvement. Utilization rate, effect of low energy consumption
- Summary
- Abstract
- Description
- Claims
- Application Information
AI Technical Summary
Problems solved by technology
Method used
Examples
Embodiment 1
[0022] A treatment method for reducing the discharge of harmful substances produced by surface treatment of aluminum products, including pre-degreasing, degreasing, water washing, and oxidation composite film-forming processes;
[0023] The formation process of the oxidation composite film is as follows: S1 Weigh 30 milliliters of glacial acetic acid with a molar concentration of 0.85 mol / liter, 80 milliliters of ethanol, and 150 milliliters of deionized water, and mix them uniformly as a solvent. The ester was slowly added to the solvent, ultrasonically dispersed for 5 minutes, and 55 ml of ammonium dihydrogen phosphate solution with a molar concentration of 0.27 mol / liter was slowly added dropwise to the ultrasonic dispersion, stirred at 35°C for 10 minutes, and the molar concentration used was 1.40 mol / L of ammonia water to adjust the pH value of the system between 6.4-6.5, at 25°C, stir at a speed of 45 rpm for 3 hours to obtain A sol for later use;
[0024] S2 Take a clea...
Embodiment 2
[0030] A treatment method for reducing the discharge of harmful substances produced by surface treatment of aluminum products, including pre-degreasing, degreasing, water washing, and oxidation composite film-forming processes;
[0031] The oxidation composite film formation process is as follows: S1 Weigh 35 milliliters of glacial acetic acid with a molar concentration of 0.88 mol / liter, 85 milliliters of ethanol, and 155 milliliters of deionized water, and mix them uniformly as a solvent. Under stirring, 36 milliliters of ethyl titanate The ester was slowly added to the solvent, ultrasonically dispersed for 7 minutes, and 58 ml of ammonium dihydrogen phosphate solution with a molar concentration of 0.28 mol / liter was slowly added dropwise to the ultrasonic dispersion, stirred at 38°C for 12 minutes, and the molar concentration used was 1.45 mol / L ammonia water to adjust the pH value of the system between 6.4-6.5, at 26°C, stir at a speed of 50 rpm for 3.5 hours to obtain A so...
Embodiment 3
[0038] A treatment method for reducing the discharge of harmful substances produced by surface treatment of aluminum products, including pre-degreasing, degreasing, water washing, and oxidation composite film-forming processes;
[0039] The formation process of the oxidation composite film is as follows: S1 Weigh 40 milliliters of glacial acetic acid with a molar concentration of 0.90 mol / liter, 90 milliliters of ethanol, and 160 milliliters of deionized water, and mix them uniformly as a solvent. The ester was slowly added to the solvent, ultrasonically dispersed for 10 minutes, and 60 ml of ammonium dihydrogen phosphate solution with a molar concentration of 0.30 mol / liter was slowly added dropwise to the ultrasonic dispersion, stirred at 40°C for 15 minutes, and the molar concentration used was 1.50 mol / L of ammonia water to adjust the pH value of the system between 6.4-6.5, at 28°C, stir at a speed of 55 rpm for 4 hours to obtain A sol for later use;
[0040] S2 Take a cle...
PUM
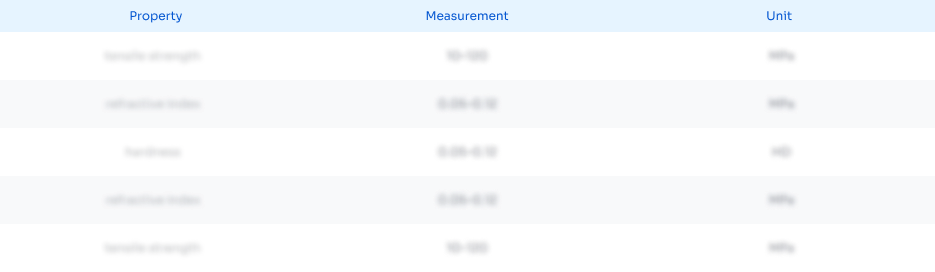
Abstract
Description
Claims
Application Information

- R&D
- Intellectual Property
- Life Sciences
- Materials
- Tech Scout
- Unparalleled Data Quality
- Higher Quality Content
- 60% Fewer Hallucinations
Browse by: Latest US Patents, China's latest patents, Technical Efficacy Thesaurus, Application Domain, Technology Topic, Popular Technical Reports.
© 2025 PatSnap. All rights reserved.Legal|Privacy policy|Modern Slavery Act Transparency Statement|Sitemap|About US| Contact US: help@patsnap.com