Preparation method of low-temperature plasma modified catalytic fiber filter material
A low-temperature plasma and plasma technology, applied in separation methods, chemical instruments and methods, catalysts for physical/chemical processes, etc., can solve the problems of low input cost and good catalytic effect, and achieve uniform loading, good denitration effect, and load good effect
- Summary
- Abstract
- Description
- Claims
- Application Information
AI Technical Summary
Problems solved by technology
Method used
Image
Examples
Embodiment 1
[0037]A method for preparing a catalytic fiber filter material modified by low-temperature plasma, comprising the following steps:
[0038] 1) Polymer pretreatment: take a certain amount of polyurethane (PUR) as the solute, use dimethylformamide (DMF) solution as the solvent to prepare a solution with a mass fraction of 15%, at a temperature of 80 ° C and a magnetic stirrer speed of Stir for 3 hours at a speed of 1300 rpm;
[0039] 2) Conductivity enhancement: Add tetraethylammonium bromide to the solution obtained in step 1) and mix in the solution. The concentration of tetraethylammonium bromide in the mixed solution is 5g / L. Stir at a high speed for 3 hours at a speed of 1300 rpm to obtain a mixed solution;
[0040] 3) Add active components: Weigh the catalyst precursor with a molar ratio of 0.5:0.4:0.07:0.03: AR purity 50% manganese nitrate solution, cerium nitrate powder, iron nitrate powder and cobalt nitrate powder, mix the catalyst precursor with the step 2) Mix and ...
Embodiment 2
[0047] A method for preparing a catalytic fiber filter material modified by low-temperature plasma, comprising the following steps:
[0048] 1) Polymer pretreatment: take a certain amount of polyurethane (PUR) as the solute, use dimethylformamide (DMF) solution as the solvent to prepare a solution with a mass fraction of 18%. Stir for 2h at a speed of 1200 rpm;
[0049] 2) Conductivity enhancement: Add tetraethylammonium bromide to the solution obtained in step 1) and mix in the solution. The concentration of tetraethylammonium bromide in the mixed solution is 8g / L. Stir at a high speed for 2 hours at a speed of 1200 rpm to obtain a mixed solution;
[0050] 3) Add active components: Weigh the catalyst precursor manganese sulfide powder, cerium chloride powder, ferric chloride powder and cobalt chloride powder at a molar ratio of 0.45:0.5:0.06:0.04, and mix the catalyst precursor with step 2) The obtained mixed solution was mixed and stirred for 40 h at a temperature of 100° ...
Embodiment 3
[0057] A method for preparing a catalytic fiber filter material modified by low-temperature plasma, comprising the following steps:
[0058] 1) Take a certain amount of polyurethane (PUR) as a solute, use dimethylformamide (DMF) solution as a solvent to prepare a solution with a mass fraction of 20%. Stir for 3 hours at a rotating speed;
[0059] 2) Conductivity enhancement: Add tetraethylammonium bromide to the solution obtained in step 1) and mix in the solution. The concentration of tetraethylammonium bromide in the mixed solution is 10g / L. Stir at a high speed of 1500 rpm for 2.5 hours to obtain a mixed solution;
[0060] 3) Add active components: Weigh a certain amount of catalyst precursor manganese acetate powder, cerium acetate powder, iron acetate powder and cobalt acetate powder at a molar ratio of 5:4:0.07:0.03, and combine the catalyst precursor with step 2) to obtain The mixed solution was mixed and stirred for 48 hours at a temperature of 80° C. and a magnetic ...
PUM
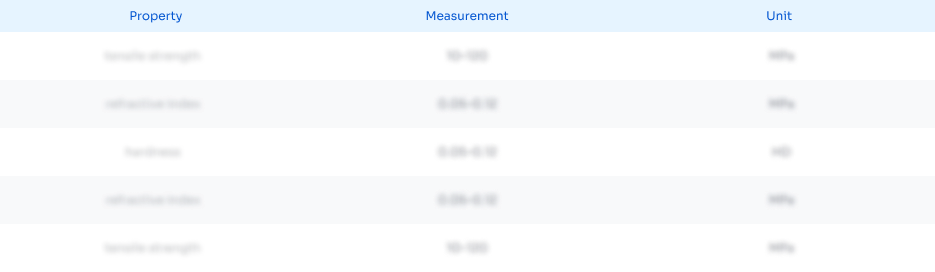
Abstract
Description
Claims
Application Information

- R&D
- Intellectual Property
- Life Sciences
- Materials
- Tech Scout
- Unparalleled Data Quality
- Higher Quality Content
- 60% Fewer Hallucinations
Browse by: Latest US Patents, China's latest patents, Technical Efficacy Thesaurus, Application Domain, Technology Topic, Popular Technical Reports.
© 2025 PatSnap. All rights reserved.Legal|Privacy policy|Modern Slavery Act Transparency Statement|Sitemap|About US| Contact US: help@patsnap.com