Refining process for producing spring steel through electric furnace
A spring steel, electric furnace smelting technology, applied in electric furnace, process efficiency improvement, furnace and other directions, can solve the problems such as difficult control of molten steel temperature fluctuation, high requirements, difficult desulfurization, etc., to maintain good reducibility and reduce the secondary molten steel. Stable effect of oxidation and electric furnace tapping deoxidation alloying composition
- Summary
- Abstract
- Description
- Claims
- Application Information
AI Technical Summary
Problems solved by technology
Method used
Image
Examples
Embodiment 1
[0027] A kind of electric furnace production refining process of spring steel of the present embodiment, its steps are:
[0028] Step 1: electric furnace smelting;
[0029] a) Using scrap steel and molten iron as raw materials, molten iron S≤0.060%, no need for pretreatment of molten iron, dephosphorization of slag flow under low temperature conditions in the early stage of electric furnace, to ensure that the finished phosphorus meets product requirements;
[0030] b) Eccentric furnace bottom tapping is adopted to prevent slag dropping, and the amount of refined phosphorus return is ≤0.005%; the tapping temperature is above 1620°C to ensure the fluidity of LF entering the top slag, and no high requirements are put forward for the carbon at the end of the electric furnace, which is convenient for electric furnace operation , to create good conditions for on-site mass production and stable production rhythm, and at the same time, it can increase the content of SiO2 in the slag,...
specific Embodiment 1
[0039] Specific embodiment 1, steel type is 55SiCr: step is as follows:
[0040] (1) Electric furnace smelting: molten iron ratio 41%, electric furnace tapping carbon 0.13%, phosphorus 0.005%, tapping temperature 1631°C, tapping amount 111 tons, calculated according to the formula, low carbon low titanium ferrosilicon theoretical addition amount is 1782 kg , the actual amount added is 1774 kg, LF’s inbound silicon is 1.01%, and phosphorus is 0.006%;
[0041] (2) LF furnace smelting: During the LF smelting process, the amount of lime added is 792 kg, the total amount of calcium carbide is 150 kg, the silicon calcium barium is 150 kg, and 70 kg of silicon carbide is added during the slag preservation period to maintain the reducibility of the top slag and the white slag retention time After 48 minutes, the composition of the final slag is shown in the table below, the basicity is 1.88, and the TFe+MnO is 0.60%;
[0042]
[0043] (3) The smelting of RH furnace adopts deep vac...
Embodiment 2
[0045] A kind of electric furnace production refining process of spring steel of the present embodiment, its steps are:
[0046](1) Electric furnace smelting: the steel type is 55SiCr, the molten iron ratio is 41%, the electric furnace tapping carbon is 0.11%, phosphorus is 0.006%, the tapping temperature is 1641°C, and the tapping amount is 110 tons. Calculated according to the formula, low carbon and low titanium ferrosilicon theory The added amount is 1771 kg, the actual added amount is 1748 kg, LF inbound silicon is 1.02%, phosphorus is 0.008%;
[0047] (2) LF furnace smelting: During the LF smelting process, the amount of lime added is 809 kg, the total amount of calcium carbide is 140 kg, the silicon calcium barium is 100 kg, and 60 kg of silicon carbide is added during the slag preservation period to maintain the reducibility of the top slag and the white slag retention time After 55 minutes, the composition of the final slag is shown in the table below, the basicity is...
PUM
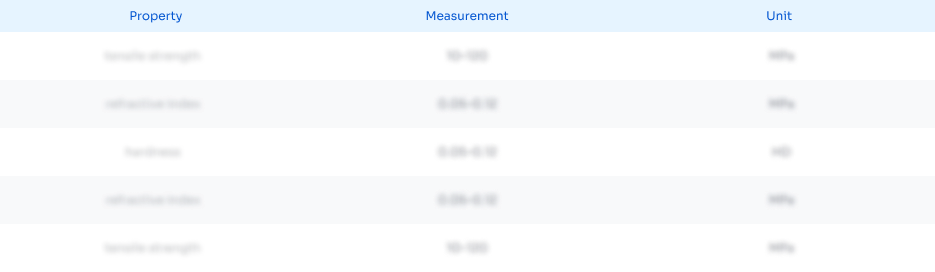
Abstract
Description
Claims
Application Information

- R&D
- Intellectual Property
- Life Sciences
- Materials
- Tech Scout
- Unparalleled Data Quality
- Higher Quality Content
- 60% Fewer Hallucinations
Browse by: Latest US Patents, China's latest patents, Technical Efficacy Thesaurus, Application Domain, Technology Topic, Popular Technical Reports.
© 2025 PatSnap. All rights reserved.Legal|Privacy policy|Modern Slavery Act Transparency Statement|Sitemap|About US| Contact US: help@patsnap.com