Welding method for vacuum electronic bundle of aluminum alloy water cooling joint
A technology of vacuum electron beam and welding method, applied in electron beam welding equipment, welding equipment, metal processing equipment, etc., can solve the problems of low surface tension, high melting point, surface depression, etc., and achieve uniform weld formation and high power density. , The effect of welding deformation is small
- Summary
- Abstract
- Description
- Claims
- Application Information
AI Technical Summary
Problems solved by technology
Method used
Image
Examples
Embodiment Construction
[0023] combined with Figure 1-3 The present invention is further described in detail.
[0024] A vacuum electron beam welding method for an aluminum alloy water-cooled joint, comprising the following steps:
[0025] The first step: chemically clean the workpiece and solder, clean in 25% NaOH for 3 minutes, and then in 15% HNO 3 +0.5% HF mixed solution to wash for 1min, and finally rinse with clean water.
[0026] The second step: drying, heat preservation in a drying oven at 120°C for 1 hour.
[0027] Step 3: Preset the solder into the assembly gap of the parts, the assembly gap is 0.4-0.6mm, the thickness of the solder is 0.4mm, and the solder is 0.3mm above the surface of the part.
[0028] Step 4: Clamp the water-cooled joint and the workpiece with tooling, and put the workpiece into the vacuum electron beam welding chamber.
[0029] Step 5: Vacuum, the vacuum degree reaches 10 -5 pa.
[0030] Step 6: Set the parameters of the girth weld. When the beam current rises,...
PUM
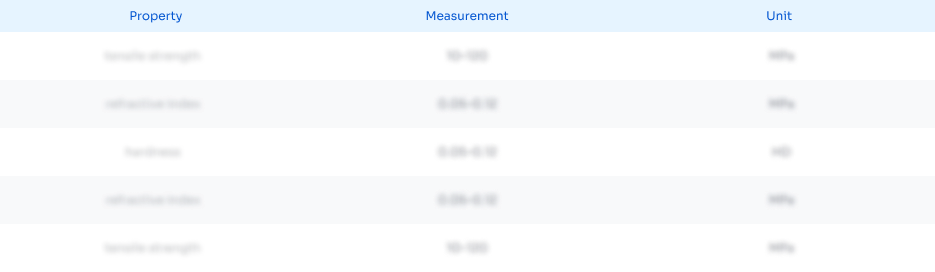
Abstract
Description
Claims
Application Information

- R&D Engineer
- R&D Manager
- IP Professional
- Industry Leading Data Capabilities
- Powerful AI technology
- Patent DNA Extraction
Browse by: Latest US Patents, China's latest patents, Technical Efficacy Thesaurus, Application Domain, Technology Topic, Popular Technical Reports.
© 2024 PatSnap. All rights reserved.Legal|Privacy policy|Modern Slavery Act Transparency Statement|Sitemap|About US| Contact US: help@patsnap.com