Copper-iron intermediate alloy and preparing method thereof
A master alloy, copper-iron technology, applied in the field of copper-iron master alloy preparation, can solve the problems of high equipment requirements, inability to ensure uniform distribution and non-segregation of iron elements, uneven composition, etc. Scale manufacturing needs, effect of improved composition uniformity
- Summary
- Abstract
- Description
- Claims
- Application Information
AI Technical Summary
Problems solved by technology
Method used
Image
Examples
Embodiment 1
[0038] A kind of copper-iron master alloy, by mass percentage, comprises following composition:
[0039] Fe: 20.1%, Ni: 0.03%, Cr: 0.06%, Mg: 0.017%, Y: 0.02%, S: 0.011%, P: 0.012%, and the balance is copper and other unavoidable trace impurities.
[0040] The preparation method of above-mentioned copper-iron master alloy comprises the steps:
[0041] (1) Batching and smelting: Batching is carried out according to the composition of copper-iron intermediate alloy. The measured pure iron sheet has a purity of 99.95% and a thickness of 0.8mm. It is cut into strips with a width of 50-60mm and a length of 400mm. Add the electrolytic copper plate to the intermediate frequency induction furnace to raise the temperature of the material, wait until it is completely melted, and the temperature rises to 1365 ° C, then start to add Ni and Cr, keep warm for 30 minutes, then gradually add pure iron sheets, add 5 to 10 pieces of iron sheets each time, After it is completely melted, add the...
Embodiment 2
[0047] A kind of copper-iron master alloy, by mass percentage, comprises following composition:
[0048] Fe: 29.7%, Ni: 0.02%, Cr: 0.06%, Mg: 0.028%, Y: 0.03%, S: 0.016%, P: 0.015%, and the balance is copper and other unavoidable trace impurities.
[0049] The preparation method of above-mentioned copper-iron master alloy comprises the steps:
[0050] (1) Batching and smelting: Batching is carried out according to the composition of copper-iron intermediate alloy. The measured pure iron sheet has a purity of 99.95% and a thickness of 0.8mm. It is cut into strips with a width of 50-60mm and a length of 400mm. Add the electrolytic copper plate to the intermediate frequency induction furnace to raise the temperature of the material, wait until it is completely melted, and the temperature rises to 1350°C, then start to add Ni and Cr, keep warm for 28 minutes, then gradually add pure iron sheets, add 5 to 10 pieces of iron sheets each time, After it is completely melted, add the n...
Embodiment 3
[0056] A kind of copper-iron master alloy, by mass percentage, described copper-iron master alloy comprises following composition:
[0057] Fe: 30.3%, Ni: 0.04%, Cr: 0.07%, Mg: 0.04%, Y: 0.045%, S: 0.022%, P: 0.022%, and the balance is copper and other unavoidable trace impurities.
[0058] The preparation method of above-mentioned copper-iron master alloy comprises the steps:
[0059] (1) Batching and smelting: Batching is carried out according to the composition of copper-iron intermediate alloy. The measured pure iron sheet has a purity of 99.95% and a thickness of 0.8mm. It is cut into strips with a width of 50-60mm and a length of 400mm. Add the electrolytic copper plate to the intermediate frequency induction furnace to raise the temperature of the material, wait until it is completely melted, and the temperature rises to 1333°C, then start to add Ni and Cr, keep warm for 30 minutes, then gradually add pure iron sheets, add 5 to 10 pieces of iron sheets each time, After...
PUM
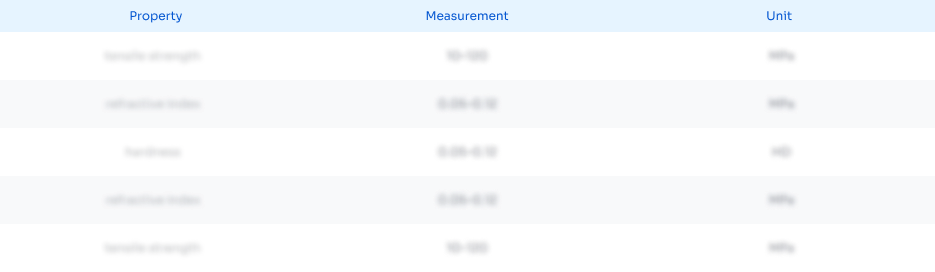
Abstract
Description
Claims
Application Information

- R&D
- Intellectual Property
- Life Sciences
- Materials
- Tech Scout
- Unparalleled Data Quality
- Higher Quality Content
- 60% Fewer Hallucinations
Browse by: Latest US Patents, China's latest patents, Technical Efficacy Thesaurus, Application Domain, Technology Topic, Popular Technical Reports.
© 2025 PatSnap. All rights reserved.Legal|Privacy policy|Modern Slavery Act Transparency Statement|Sitemap|About US| Contact US: help@patsnap.com