Preparation method of high-strength structural color fibers
A structural color, high-strength technology, used in carbon fiber, fiber processing, textiles and papermaking, etc., can solve the problem that the mechanical properties of structural color fibers do not meet the requirements of wear, improve aging resistance and chemical resistance, and improve strength. Effect
- Summary
- Abstract
- Description
- Claims
- Application Information
AI Technical Summary
Problems solved by technology
Method used
Examples
Embodiment 1
[0039] Wash styrene with a mass fraction of 10% sodium hydroxide solution for 3 times, and separate the upper oily liquid with a separatory funnel, repeat the above operation until it is colorless, and then obtain the reaction solution, wash the reaction solution with deionized water to the water layer If it is neutral, then the washing solution is obtained. Mix and dry anhydrous calcium chloride and the washing solution according to the mass ratio of 1:3. Distill under reduced pressure at a temperature of 40°C and a pressure of 18mmHg, and collect fractions to obtain pretreated styrene; Mix ammonium persulfate, poly-N-isopropylacrylamide and deionized water at a mass ratio of 1:10:3, and adjust the pH value to 8.0 with a mass fraction of 1% sodium hydroxide solution to obtain a mixed solution. Mix the pretreated styrene with the mixed solution at a ratio of 1:3, and bubble it at room temperature for 20 minutes under a nitrogen atmosphere to obtain a matrix liquid. Stir the mat...
Embodiment 2
[0041] Wash styrene with a mass fraction of 10% sodium hydroxide solution for 4 times, and separate the upper oily liquid with a separatory funnel, repeat the above operation until it is colorless, and obtain the reaction solution, wash the reaction solution with deionized water to the water layer It is neutral to obtain the washing solution. Mix and dry anhydrous calcium chloride and the washing solution according to the mass ratio of 1:3. Distill under reduced pressure at a temperature of 42°C and a pressure of 19 mmHg to collect fractions to obtain pretreated styrene; Mix ammonium persulfate, poly-N-isopropylacrylamide and deionized water at a mass ratio of 1:10:3, and adjust the pH value to 8.1 with a mass fraction of 1% sodium hydroxide solution to obtain a mixed solution. Mix the pretreated styrene with the mixed solution at a ratio of 1:3, and bubble it at room temperature for 25 minutes under a nitrogen atmosphere to obtain a matrix liquid. Stir the matrix liquid at a t...
Embodiment 3
[0043] Wash styrene with a mass fraction of 10% sodium hydroxide solution 5 times, and separate the upper oily liquid with a separatory funnel, repeat the above operation until it is colorless, and then obtain the reaction solution, wash the reaction solution with deionized water to the water layer It is neutral to obtain the washing liquid, and the anhydrous calcium chloride and the washing liquid are mixed and dried at a temperature of 44 ° C and a pressure of 20 mmHg according to the mass ratio of 1:3, and the fraction is collected to obtain pretreated styrene; Mix ammonium persulfate, poly-N-isopropylacrylamide and deionized water at a mass ratio of 1:10:3, and adjust the pH value to 8.2 with a mass fraction of 1% sodium hydroxide solution to obtain a mixed solution. Mix the pretreated styrene with the mixed solution at a ratio of 1:3, and bubble it at room temperature for 30 minutes under a nitrogen atmosphere to obtain a matrix liquid. Stir the matrix liquid at a temperat...
PUM
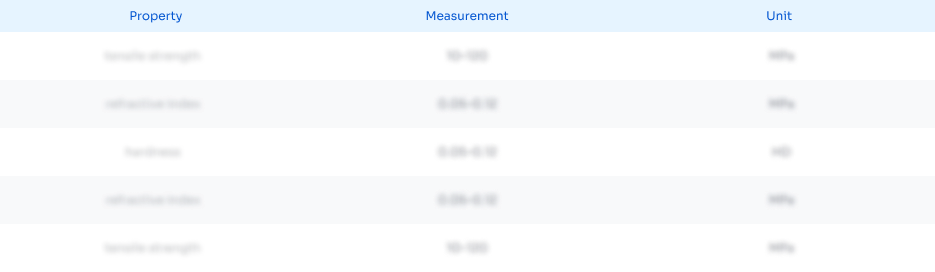
Abstract
Description
Claims
Application Information

- R&D Engineer
- R&D Manager
- IP Professional
- Industry Leading Data Capabilities
- Powerful AI technology
- Patent DNA Extraction
Browse by: Latest US Patents, China's latest patents, Technical Efficacy Thesaurus, Application Domain, Technology Topic, Popular Technical Reports.
© 2024 PatSnap. All rights reserved.Legal|Privacy policy|Modern Slavery Act Transparency Statement|Sitemap|About US| Contact US: help@patsnap.com