Preparation method of anti-crack low-shrinkage cement mortar
A cement mortar and low shrinkage technology, applied in the field of cement mortar materials, can solve the problems of low compressive strength, poor crack resistance, and easy microcracks, etc., and achieve the effect of improving dispersion performance and improving hydrophilicity
- Summary
- Abstract
- Description
- Claims
- Application Information
AI Technical Summary
Problems solved by technology
Method used
Examples
Embodiment 1
[0029] Preparation of coarse wood flour:
[0030] Take 200g of straw residue and 400mL of sodium hydroxide solution with a mass fraction of 45% and put them into a water bath reactor with a stirrer, heat the water bath to 90°C, start the stirrer, stir for 3h, filter, remove the filter residue and use the obtained filtrate The glacial acetic acid with a mass fraction of 95% was neutralized to neutral to obtain a lignin suspension, which was centrifuged at a high speed of 3500r / min for 12 minutes to remove the supernatant and separate the lower precipitate, which was washed twice with water and placed in In an oven with a set temperature of 70°C, dry for 4 hours to obtain coarse wood powder;
[0031] Preparation of product:
[0032] In parts by weight, add 70 parts of β-cyclodextrin and 100 parts of sodium hydroxide solution with a mass fraction of 90% to the beaker, stir at room temperature for 10 minutes, then add 5 parts of glycidyl trimethyl chloride Ammonium, put the beaker...
Embodiment 2
[0040] Preparation of coarse wood flour:
[0041] Take 215g of straw residue and 425mL of sodium hydroxide solution with a mass fraction of 45% and put them into a water bath reaction kettle with a stirrer, heat the water bath to 92.5°C, start the stirrer, stir for 4h, filter, remove the filter residue and use the obtained filtrate The glacial acetic acid with a mass fraction of 95% was neutralized to neutral to obtain a lignin suspension, which was centrifuged at a high speed of 3600r / min for 13.5min to remove the supernatant and separate the lower precipitate, which was washed with water for 2.5 times and placed in In an oven with a set temperature of 75°C, dry for 4.5 hours to obtain coarse wood powder;
[0042] Preparation of product:
[0043] In parts by weight, add 72.5 parts of β-cyclodextrin and 115 parts of sodium hydroxide solution with a mass fraction of 90% to the beaker, stir at room temperature for 12.5 minutes, and then add 7.5 parts of epoxypropyl trimethyl ch...
Embodiment 3
[0051] Preparation of coarse wood flour:
[0052] Take 230g of straw residue and 450mL of sodium hydroxide solution with a mass fraction of 45% and put them into a water bath reactor with a stirrer, heat the water bath to 95°C, start the stirrer, stir for 5h, filter, remove the filter residue and use the obtained filtrate The glacial acetic acid with a mass fraction of 95% was neutralized to neutral to obtain a lignin suspension, which was centrifuged at a high speed of 3700r / min for 15 minutes to remove the supernatant and separate the lower precipitate, which was washed with water for 3 times and placed in In an oven with a set temperature of 80°C, dry for 5 hours to obtain coarse wood powder;
[0053] Preparation of product:
[0054] In parts by weight, add 75 parts of β-cyclodextrin and 130 parts of sodium hydroxide solution with a mass fraction of 90% to the beaker, stir at room temperature for 15 minutes, then add 10 parts of glycidyl trimethyl chloride ammonium, place...
PUM
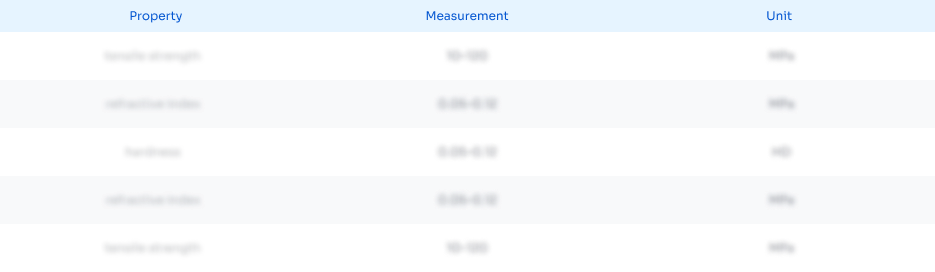
Abstract
Description
Claims
Application Information

- Generate Ideas
- Intellectual Property
- Life Sciences
- Materials
- Tech Scout
- Unparalleled Data Quality
- Higher Quality Content
- 60% Fewer Hallucinations
Browse by: Latest US Patents, China's latest patents, Technical Efficacy Thesaurus, Application Domain, Technology Topic, Popular Technical Reports.
© 2025 PatSnap. All rights reserved.Legal|Privacy policy|Modern Slavery Act Transparency Statement|Sitemap|About US| Contact US: help@patsnap.com