Preparation method and separation method of low polymerization cyclic polymer
A technology of cyclic polymers and separation methods, applied in the direction of organic chemistry, can solve the problems of increasing production costs, non-compliance, non-compliance with atom economy, and environmental protection.
- Summary
- Abstract
- Description
- Claims
- Application Information
AI Technical Summary
Problems solved by technology
Method used
Image
Examples
Embodiment 1
[0187] Example 1 Synthesis of Mixture 1
[0188] Add 6.15g of terephthaloyl chloride and 21.84g of 1,4-butanediol into 30ml of tetrahydrofuran, cool to 0~10℃ under stirring, and add dropwise triethylamine tetrahydrofuran solution (12.26g triethylamine dissolved in 10ml Tetrahydrofuran), after the dropwise addition, stir at room temperature for 12 hours, the reaction is over, the reaction solution is poured into 120ml of water, extracted with 40ml of dichloromethane, and then repeated extraction operation twice, combined the organic phase, the organic phase was used in turn with 50ml 10% hydrochloric acid solution , 50ml saturated sodium bicarbonate solution and saturated brine washed, dried over anhydrous sodium sulfate, evaporated under reduced pressure to remove the solvent, and dried to obtain 7.17g off-white mixture 1 solid. The high performance liquid chromatography of this mixture is shown in Figure 13 .
[0189] The crude product is calculated based on the output of 5g ter...
Embodiment 2
[0190] Example 2 Selection of reaction solvent for synthesis mixture 1
[0191] In order to investigate the influence of different reaction solvents on the synthesis mixture 1, the reaction solvent (tetrahydrofuran) in Example 1 was replaced with N,N-dimethylformamide, acetonitrile, dichloromethane and chloroform, and other reaction conditions remained unchanged , The influence of different reaction solvents on the reaction is shown in Table 1:
[0192] Table 1 The influence of different reaction solvents on synthesis mixture 1
[0193] Serial number Reaction solvent Output (g) Product color 1 Tetrahydrofuran7.17 Off-white 2 N,N-Dimethylformamide5.88 Off-white 3 Acetonitrile7.08 Off-white 4 Dichloromethane4.68 Off-white 5 Trichloromethane4.29 Off-white
[0194] It can be seen from Table 1 that when tetrahydrofuran, N,N-dimethylformamide, acetonitrile, dichloromethane and chloroform are used as the reaction solvent, a white-like mixture 1 solid can be obtained, and when tetrahydr...
Embodiment 3
[0195] Example 3 Selection of reaction concentration of synthesis mixture 1
[0196] In order to investigate the influence of different reaction concentrations on the synthesis mixture 1, the amount of reaction solvent (tetrahydrofuran) added in Example 1 was adjusted to be based on terephthaloyl chloride. The reaction concentration was changed. Other reaction conditions remained unchanged. The impact of the reaction is shown in Table 2:
[0197] Table 2 The influence of different reaction concentrations on synthetic mixture 1
[0198] Serial number Addition of tetrahydrofuran (ml) Reaction concentration (g / ml) Output (g) Product color 1400.157.17 Off-white 2600.16.55 Off-white 3200.27.11 Light Brown
[0199] It can be seen from Table 2 that based on terephthaloyl chloride, when the reaction concentration is 0.15g / ml, 0.1g / ml, 0.2g / ml, the solid of off-white mixture 1 can be obtained, and when the reaction concentration increases When it reaches 0.2g / ml, the color of the produc...
PUM
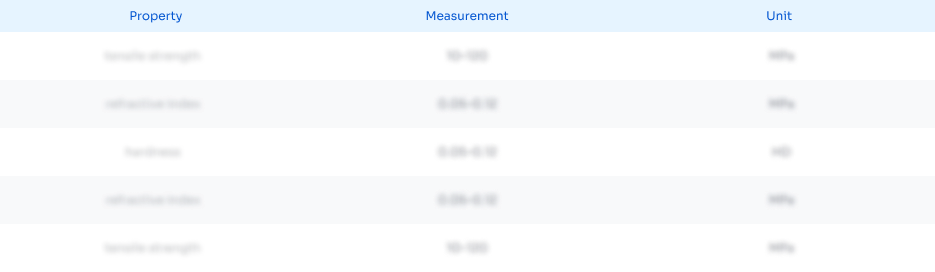
Abstract
Description
Claims
Application Information

- R&D Engineer
- R&D Manager
- IP Professional
- Industry Leading Data Capabilities
- Powerful AI technology
- Patent DNA Extraction
Browse by: Latest US Patents, China's latest patents, Technical Efficacy Thesaurus, Application Domain, Technology Topic, Popular Technical Reports.
© 2024 PatSnap. All rights reserved.Legal|Privacy policy|Modern Slavery Act Transparency Statement|Sitemap|About US| Contact US: help@patsnap.com