High silica/phenolic aldehyde material with excellent ablation resistance and heat insulation performance and preparing method thereof
An ablation-resistant, high-silicon-oxygen technology, applied in the field of composite materials, to achieve the effects of improved mechanical properties, small thickness and low density
- Summary
- Abstract
- Description
- Claims
- Application Information
AI Technical Summary
Problems solved by technology
Method used
Image
Examples
Embodiment 1
[0013] Raw material components (by mass percentage): boron phenolic resin 38%, high silica fiber 50%, alumina airgel powder 2%, potassium hexatitanate whisker 6%, SiC micropowder 4%;
[0014] Preparation process: Dissolve boron phenolic resin in absolute ethanol at a volume ratio of 1:10, stir and disperse evenly; then add high silica fiber, alumina airgel powder, potassium hexatitanate whisker and SiC micropowder in sequence and stir Disperse evenly; then dry at 60°C for 24 hours, remove the solvent ethanol to obtain a fiber prepreg; finally put the fiber prepreg into a mold, heat press at 200°C and 30MPa, cool, and demould, that is, a good High silica / phenolic composite material with ablation resistance and thermal insulation properties. Its physical and chemical properties are listed in Table 1.
Embodiment 2
[0016] Raw material components (by mass percentage): boron phenolic resin 33%, high silica fiber 56%, silica airgel powder 1%, potassium hexatitanate whisker 8%, SiC micropowder 2%;
[0017] Preparation process: Dissolve boron phenolic resin in absolute ethanol at a volume ratio of 1:15, stir and disperse evenly; then add high silica fiber, alumina airgel powder, potassium hexatitanate whisker and SiC micropowder in sequence and stir Disperse evenly; then dry at 80°C for 24 hours, remove the solvent ethanol to obtain a fiber prepreg; finally put the fiber prepreg into a mold, heat press it at 180°C and 20MPa, cool, and demould, that is, a good High silica / phenolic composite material with ablation resistance and thermal insulation properties. Its physical and chemical properties are listed in Table 1.
Embodiment 3
[0019] Raw material components (by mass percentage): boron phenolic resin 42%, high silica fiber 45%, alumina airgel powder 5%, potassium hexatitanate whisker 3%, SiC micropowder 5%;
[0020] Preparation process: Dissolve boron phenolic resin in absolute ethanol at a volume ratio of 1:12, stir and disperse evenly; then add high silica fiber, alumina airgel powder, potassium hexatitanate whisker and SiC micropowder in sequence and stir Disperse evenly; then dry at 100°C for 24 hours, remove the solvent ethanol to obtain a fiber prepreg; finally put the fiber prepreg into a mold, heat press it at 185°C, 10MPa, cool, and demould, that is, a good High silica / phenolic composite material with ablation resistance and thermal insulation properties. Its physical and chemical properties are listed in Table 1.
PUM
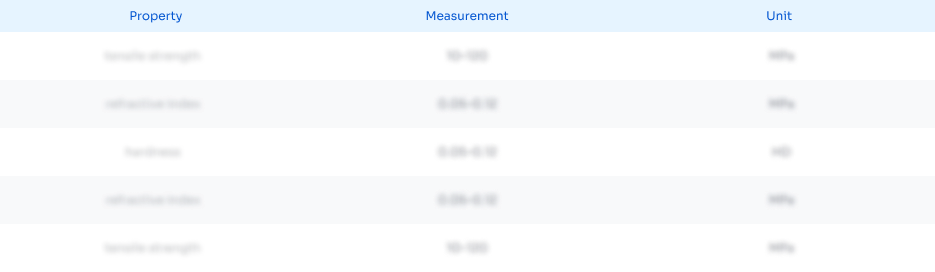
Abstract
Description
Claims
Application Information

- R&D Engineer
- R&D Manager
- IP Professional
- Industry Leading Data Capabilities
- Powerful AI technology
- Patent DNA Extraction
Browse by: Latest US Patents, China's latest patents, Technical Efficacy Thesaurus, Application Domain, Technology Topic, Popular Technical Reports.
© 2024 PatSnap. All rights reserved.Legal|Privacy policy|Modern Slavery Act Transparency Statement|Sitemap|About US| Contact US: help@patsnap.com