Ultraviolet light-emitting element, ultraviolet light-emitting element packaging body and manufacturing method thereof
A technology of light-emitting components and packages, which is applied in the direction of electrical components, semiconductor devices, circuits, etc., can solve problems such as reflow soldering bubbles, cutting off, vibration off, etc., to prevent easy cracking, increase light output efficiency, increase adhesion or adhesion sexual effect
- Summary
- Abstract
- Description
- Claims
- Application Information
AI Technical Summary
Problems solved by technology
Method used
Image
Examples
Embodiment 1
[0049] The invention provides a package body of an ultraviolet semiconductor light-emitting element, which belongs to the technical field of LED light-emitting. Such as figure 1 As shown, the package includes a substrate 101 on which a flip-chip ultraviolet semiconductor light-emitting element is mounted.
[0050] In this embodiment, the substrate 101 is formed of any material. For example, metals, ceramics, resins, dielectrics, pulp, glass, paper, composites thereof, or composites of these materials and conductive materials (eg, metals, carbon, etc.) may be mentioned. Metals include metals containing copper, iron, nickel, chromium, aluminum, silver, gold, titanium or alloys thereof. Examples of resins include epoxy resins, bismaleimide triazine (BT) resins, polyimide resins, and the like. The resin may contain white pigments such as titanium oxide. Among them, ceramics are preferable.
[0051] Examples of ceramics include those containing aluminum oxide, aluminum nitrid...
Embodiment 2
[0095] As an alternative to Embodiment 1, this embodiment provides Figure 10 In the schematic diagram of the structure of the ultraviolet semiconductor light-emitting element shown, the second surface side of the light-transmitting substrate 104 includes a first region 1041, and the height of the uneven pattern on the surface of the first region is H4, and the range of H4 is 0.1-2 μm. The thickness from the rough pattern surface to the first surface side of the substrate is H5, the thickness of H5 is more than 250 μm, the second surface side includes a second region 1042, and the surface of the second region 1042 is Relatively flat, relatively flat may be absolutely flat or the height of the uneven topography is less than 5nm. The thickness H6 from the surface of the second region 1042 on the second surface side to the first surface side is H6, the thickness H6 of the second region 1042 is lower than H5 of the first region 1041, and the difference between H5 and H4 is larger ...
PUM
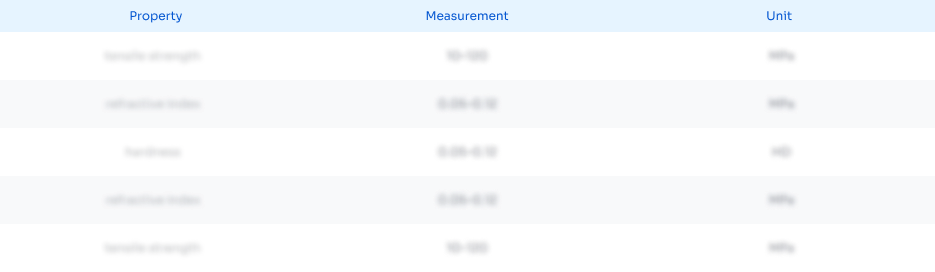
Abstract
Description
Claims
Application Information

- R&D
- Intellectual Property
- Life Sciences
- Materials
- Tech Scout
- Unparalleled Data Quality
- Higher Quality Content
- 60% Fewer Hallucinations
Browse by: Latest US Patents, China's latest patents, Technical Efficacy Thesaurus, Application Domain, Technology Topic, Popular Technical Reports.
© 2025 PatSnap. All rights reserved.Legal|Privacy policy|Modern Slavery Act Transparency Statement|Sitemap|About US| Contact US: help@patsnap.com