Method for preparing vanadyl oxalate from vanadium slag through short process
A technology of vanadyl oxalate and vanadyl oxalate solid, which is applied in the direction of carboxylate preparation, carboxylate preparation, chemical instruments and methods, etc., and can solve the problems of high production cost, long process flow, complex vanadyl oxalate process, etc. Achieve the effect of low production cost and short process
- Summary
- Abstract
- Description
- Claims
- Application Information
AI Technical Summary
Problems solved by technology
Method used
Examples
Embodiment 1
[0027] The vanadium slag comprising the composition listed in Table 1 is crushed to 0.074mm and accounts for 70%. 100g of vanadium slag is mixed with 10g of calcium carbonate. ℃, the roasting time is 60min; add 200ml pure water to the clinker obtained by roasting, add 40g oxalic acid to control the pH of the system to 3.7, control the leaching temperature at 90℃, stir and leaching for 60min, filter to obtain the vanadium-containing leaching solution and residue; the vanadium-containing solution Carry out concentrated crystallization, and obtain vanadyl oxalate solid after solid-liquid separation.
[0028] The vanadyl oxalate solid prepared in this embodiment is detected by ICP, and its purity is 99.13wt%.
Embodiment 2
[0030] The vanadium slag comprising the ingredients listed in Table 1 is crushed to 0.074mm and accounts for 80%, 100g of vanadium slag is mixed with 8g of calcium oxide, and then the resulting mixture is added to a muffle furnace and fed with air for high-temperature roasting, and the roasting temperature is controlled to be 950 ℃, the roasting time is 100min; add 300ml pure water to the clinker obtained by roasting, add 30g oxalic acid to control the pH of the system to 4.6, control the leaching temperature at 90℃, stir and leaching for 45min, filter to obtain the vanadium-containing leaching solution and residue; the vanadium-containing solution Carry out concentrated crystallization, and obtain vanadyl oxalate solid after solid-liquid separation.
[0031] The vanadyl oxalate solid prepared in this embodiment is detected by ICP, and its purity is 99.57wt%.
Embodiment 3
[0033] The vanadium slag containing the ingredients listed in Table 1 is crushed to 0.074mm, accounting for 85%. Take 100g of vanadium slag and put air into the muffle furnace for high-temperature roasting. The roasting temperature is controlled to be 900°C, and the roasting time is 120min; Add 400ml of pure water to the material, add 40g of oxalic acid to control the pH of the system to 3.1, control the leaching temperature at 60°C and stir for 30 minutes, filter to obtain the vanadium-containing leachate and residue; concentrate and crystallize the vanadium-containing solution, and obtain oxalic acid oxygen after solid-liquid separation. Vanadium solid
[0034] The vanadyl oxalate solid prepared in this embodiment is detected by ICP, and its purity is 99.82wt%.
PUM
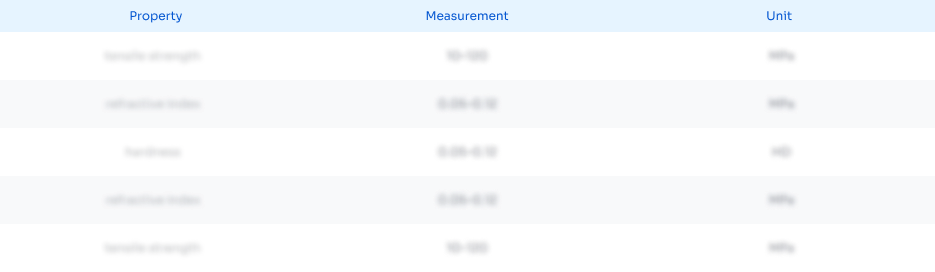
Abstract
Description
Claims
Application Information

- R&D
- Intellectual Property
- Life Sciences
- Materials
- Tech Scout
- Unparalleled Data Quality
- Higher Quality Content
- 60% Fewer Hallucinations
Browse by: Latest US Patents, China's latest patents, Technical Efficacy Thesaurus, Application Domain, Technology Topic, Popular Technical Reports.
© 2025 PatSnap. All rights reserved.Legal|Privacy policy|Modern Slavery Act Transparency Statement|Sitemap|About US| Contact US: help@patsnap.com