Production method of toughened polyurethane film
A polyurethane film and polyurethane technology, which is applied in the field of preparation of toughened polyurethane film, can solve the problems of not giving full play to the structure and performance of the polyurethane body material, the effect of polyurethane toughening is not significant enough, and the toughening range of polyurethane film is not large enough, etc.
- Summary
- Abstract
- Description
- Claims
- Application Information
AI Technical Summary
Problems solved by technology
Method used
Image
Examples
preparation example Construction
[0037] see figure 1 Shown, the invention provides a kind of preparation method of toughened polyurethane film, comprises the following steps:
[0038] S1, the preparation of film casting solution; mix the poor solvent of polyurethane, N, N-dimethylformamide and the solvent with polarity lower than N, N-dimethylformamide into a ternary mixed solvent, wherein, the polyurethane The mass fraction of poor solvent is 5% to 45%; the mass fraction of N, N-dimethylformamide is 30% to 90%; the mass fraction of solvents with lower polarity than N, N-dimethylformamide is 5% to 30%;
[0039] Then the polyurethane prepolymer and ternary mixed solvent with a mass fraction ratio of 5%: 95% to 40%: 60% are uniformly stirred mechanically and then vacuum defoamed to prepare polyurethane casting liquid; wherein, the stirring temperature is 20 to 45 ℃, the stirring rate is 500~4000r / min, and the stirring time is 0.5~5h;
[0040] S2, coagulation bath preparation;
[0041] S3, scraping and coati...
Embodiment 1
[0055] The mass fraction ratio is 5%: 85%: 10% toluene, N, N-dimethylformamide and dioxane are blended into a ternary mixed solvent, and then the mass fraction ratio is 10%: 90% Polyether polyurethane prepolymer and ternary mixed solvent were mechanically stirred for 2 hours, and then vacuum defoamed to prepare polyurethane casting solution. Wherein, the stirring temperature is 30° C., and the stirring rate is 800 r / min.
[0056] The mass fraction ratio is 99%: 1% deionized water and ethanol are compounded, stirred evenly and then prepared into a coagulation bath. Wherein, the conductivity of the deionized water is 16MΩ·cm, and the temperature of the coagulation bath solution is 20°C.
[0057] Scrape-coat the prepared polyurethane casting solution on the polytetrafluoroethylene mold, immediately immerse in the coagulation bath for 4 hours after heat treatment for 60 seconds, take it out, and then place it in a 30°C drying oven for solvent evaporation treatment for 48 hours, a...
Embodiment 2 Embodiment 8
[0063] The difference between embodiment two to embodiment eight and embodiment one is only: in the ternary mixed solvent, the mass fraction ratio of toluene, N,N-dimethylformamide and dioxane is different, and other steps are the same as in embodiment one are basically the same, and are not repeated here; the mass fractions of toluene, N, N-dimethylformamide and dioxane in embodiment two to embodiment eight are as shown in the following table:
[0064]
[0065] The process of preparing polyurethane film by traditional immersion precipitation method is: the preparation of casting solution; dissolving polyurethane in N, N-dimethylformamide, stirring uniformly after mechanical stirring, vacuum defoaming and preparing polyurethane casting solution; The casting solution is scraped and coated on the mold, and then the mold containing the casting solution is immersed in a water coagulation bath for about 2 hours, and then the mold is taken out and dried to obtain a polyurethane fi...
PUM
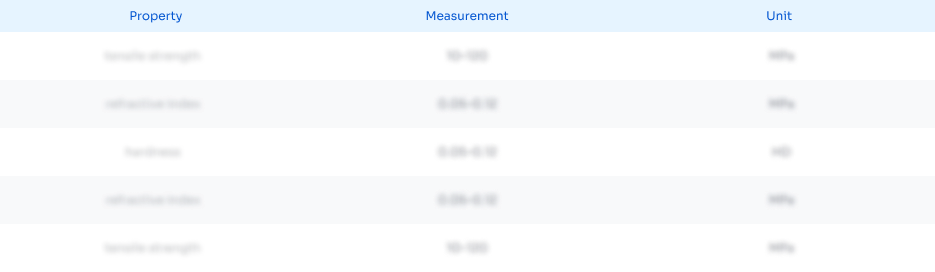
Abstract
Description
Claims
Application Information

- R&D Engineer
- R&D Manager
- IP Professional
- Industry Leading Data Capabilities
- Powerful AI technology
- Patent DNA Extraction
Browse by: Latest US Patents, China's latest patents, Technical Efficacy Thesaurus, Application Domain, Technology Topic, Popular Technical Reports.
© 2024 PatSnap. All rights reserved.Legal|Privacy policy|Modern Slavery Act Transparency Statement|Sitemap|About US| Contact US: help@patsnap.com