Coating layer for high-efficient combination of nuclear reactor and preparation method of coating layer
A nuclear reactor and cladding technology, applied in coating, sputtering, ion implantation, etc., can solve problems such as potential safety hazards, achieve good corrosion resistance, good control of composition and phase structure, and good film-base synergy Effect of deformation and high temperature oxidation resistance
- Summary
- Abstract
- Description
- Claims
- Application Information
AI Technical Summary
Problems solved by technology
Method used
Image
Examples
Embodiment 1
[0044] In this embodiment, the following preparation method is used to coat the Zr-Cr / Cr cladding layer on the outer surface of the Zr-4 alloy tube, and the specific operation steps are:
[0045] Setp1, Zr-4 alloy substrate outer surface pretreatment:
[0046] Use the Zr-4 finished tube that meets the technical specifications of the reactor cladding material, first perform ultrasonic cleaning with acetone solution for 30 minutes, then rinse with deionized water in large quantities, and then put it in a special high-vacuum drying room and dry it at 110°C for 30 minutes .
[0047] Setp2, ion cleaning of Zr-4 alloy substrate surface before deposition:
[0048] Put the dried Zr-4 alloy matrix into the furnace cavity, the base distance of the target in the furnace cavity is 100mm, and vacuumize to 3.0×10 -3 After Pa, start heating to 350°C, then fill in an appropriate amount of Ar gas to make the pressure reach 0.5Pa, adjust the duty cycle to 50%, and apply a high bias voltage of -...
Embodiment 2
[0058] In this embodiment, the following preparation method is used to coat the outer surface of the Zr-4 alloy tube with a Ti-Cr / Cr cladding layer, and the specific operation steps are:
[0059] Setp1, Zr-4 alloy substrate outer surface pretreatment:
[0060] Use the Zr-4 finished tube that meets the technical specifications of the reactor cladding material, first perform ultrasonic cleaning with acetone solution for 30 minutes, then rinse with deionized water in large quantities, and then put it in a special high-vacuum drying room and dry it at 120°C for 30 minutes .
[0061] Setp2, ion cleaning of Zr-4 alloy substrate surface before deposition:
[0062] Put the dried Zr-4 alloy into the furnace chamber, the base distance of the furnace chamber target is 120mm, and vacuumize to 5.0×10 -3 After Pa, start heating to 450°C, then fill in an appropriate amount of Ar gas to make the air pressure reach 2Pa, the high bias voltage is -200V, the current of the bunching coil is 8A, ...
Embodiment 3
[0072] In this embodiment, the following preparation method is used to coat the outer surface of the N36 alloy tube with a Zr-Cr / Cr cladding layer, and the specific operation steps are:
[0073] Setp1, N36 alloy substrate outer surface pretreatment:
[0074] N36 finished tubes that meet the technical specifications of the reactor cladding materials were used, first cleaned by ultrasonic cleaning with acetone solution for 30 minutes, then rinsed with deionized water in large quantities, and then dried in a special high-vacuum drying room at 110°C for 3 minutes.
[0075] Setp2, ion cleaning of N36 alloy substrate surface before deposition:
[0076] Put the dried N36 alloy substrate into the furnace cavity, the target base distance of the furnace cavity is 100mm, and vacuumize to 3.0×10 -3 After Pa, start heating to 350°C, then fill in an appropriate amount of Ar gas to make the pressure reach 0.5Pa, adjust the duty cycle to 50%, and apply a high bias voltage of -500V to -900V f...
PUM
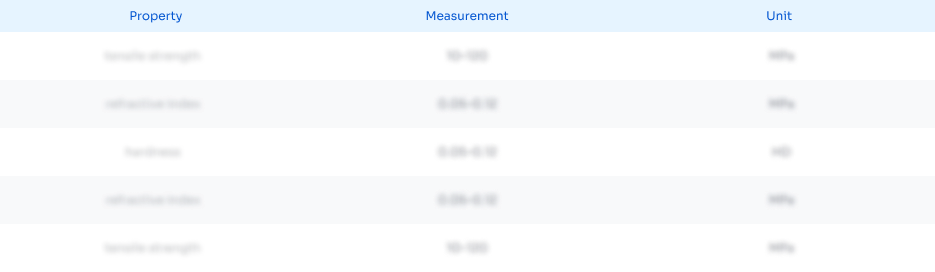
Abstract
Description
Claims
Application Information

- Generate Ideas
- Intellectual Property
- Life Sciences
- Materials
- Tech Scout
- Unparalleled Data Quality
- Higher Quality Content
- 60% Fewer Hallucinations
Browse by: Latest US Patents, China's latest patents, Technical Efficacy Thesaurus, Application Domain, Technology Topic, Popular Technical Reports.
© 2025 PatSnap. All rights reserved.Legal|Privacy policy|Modern Slavery Act Transparency Statement|Sitemap|About US| Contact US: help@patsnap.com