Preparation method of graphene-based thermal-oxidation-resistant V-belt coated composite rubber
A graphene-based, composite rubber technology, applied in the field of V-belts, can solve the problems of reinforcement, corrosion resistance and heat dissipation, and achieve the effect of increasing heat resistance, improving thermal oxidation resistance, and overcoming difficulty in dispersion.
- Summary
- Abstract
- Description
- Claims
- Application Information
AI Technical Summary
Problems solved by technology
Method used
Examples
Embodiment 1
[0034] (1) Cut 1 weight part of chloroprene rubber into small pieces less than 0.5cm, add 10 weight parts of toluene, and place it in a closed container for 72h to form a naturally flowing slurry; then add 3 weight parts of graphene, 0.5 Parts by weight of emulsifying agent sodium lauryl sulfate, stirred 10min with the rotating speed of 200rpm in airtight container, obtains graphene slurry;
[0035] (2) Add 10 parts by weight of zinc acetylacetonate and 10 parts by weight of ammonia water to the graphene slurry obtained in step (1), heat to 80°C in a closed container and stir at a high speed of 600rpm for 30min; then add 5 parts by weight of For needle-shaped wollastonite fibers, raise the temperature of the airtight container to 180°C, stir at a low speed of 50 rpm, and at the same time vacuum pump to remove volatile matter, and dry for 25 minutes to obtain a dry fluffy powder;
[0036] (3) the powder obtained in step (2) is crushed and loosened through a vortex airflow pulve...
Embodiment 2
[0039] (1) 1 weight part neoprene rubber is cut into the fritter less than 0.5cm, adds in 10 weight parts toluene, places 72h in airtight container, forms the slurry that can flow naturally; Then adds 5 weight parts graphene, 1 Parts by weight of emulsifying agent sodium lauryl sulfate, stirred 10min with the rotating speed of 200rpm in airtight container, obtains graphene slurry;
[0040] (2) Add 10 parts by weight of zinc acetate and 10 parts by weight of ammonia water to the graphene slurry obtained in step (1), heat to 80°C in a closed container and stir at a high speed of 800rpm for 45min; then add 8 parts by weight of water For magnesium stone fiber, raise the temperature of the airtight container to 180°C, stir at a low speed of 50rpm, and at the same time vacuum the volatile matter until a dry and fluffy powder is obtained;
[0041] (3) the powder obtained in step (2) is crushed and loosened through a vortex airflow pulverizer to obtain inorganic fibers adhering to the...
Embodiment 3
[0044] (1) 2 parts by weight of chloroprene rubber are cut into fritters less than 0.5cm, add in 20 parts by weight of toluene, place 72h in an airtight container, form a slurry that can flow naturally; then add 5 parts by weight of graphene, 1 Parts by weight of emulsifying agent sodium lauryl sulfate, stirred 10min with the rotating speed of 200rpm in airtight container, obtains graphene slurry;
[0045] (2) Add 8 parts by weight of zinc chloride and 15 parts by weight of ammonia to the graphene slurry obtained in step (1), heat to 80°C in a closed container and stir at a high speed of 900rpm for 30min; then add 10 parts by weight of For calcium carbonate whiskers, raise the temperature of the airtight container to 180°C, stir at a low speed of 100rpm, and at the same time vacuum pump to remove volatile matter until a dry fluffy powder is obtained;
[0046] (3) the powder obtained in step (2) is crushed and loosened through a vortex airflow pulverizer to obtain inorganic fib...
PUM
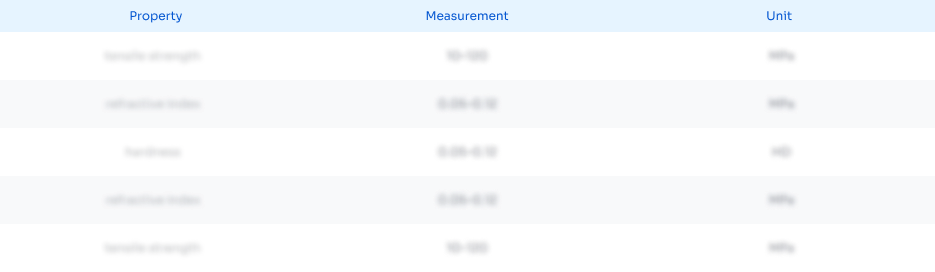
Abstract
Description
Claims
Application Information

- R&D
- Intellectual Property
- Life Sciences
- Materials
- Tech Scout
- Unparalleled Data Quality
- Higher Quality Content
- 60% Fewer Hallucinations
Browse by: Latest US Patents, China's latest patents, Technical Efficacy Thesaurus, Application Domain, Technology Topic, Popular Technical Reports.
© 2025 PatSnap. All rights reserved.Legal|Privacy policy|Modern Slavery Act Transparency Statement|Sitemap|About US| Contact US: help@patsnap.com