High-elasticity softening fuzzy agent
A fluffing agent and high-elasticity technology, which is applied in textiles, papermaking, fiber treatment, etc., can solve the problems of poor elasticity and softness improvement of knitted flannelette, achieve enhanced interface treatment effect, improve stability, and reduce interface impedance Effect
- Summary
- Abstract
- Description
- Claims
- Application Information
AI Technical Summary
Problems solved by technology
Method used
Image
Examples
preparation example Construction
[0028] The preparation method of composite softening material comprises the following steps:
[0029] (1) Take serpentine at a mass ratio of 8~13:1, add castor oil to a mortar and mix, grind at 350~550r / min for 2~4 hours to obtain abrasives, and take abrasives at a mass ratio of 15~25:1: 0.2~0.5:40 Add stearic acid amide, silane coupling agent KH-560, and reagent A to mix, shear and disperse at 3000~5000r / min for 12~20min to obtain a dispersion, take the dispersion according to the mass ratio of 5~8: 2:1 Add polytetrahydrofuran and dibutyltin dilaurate to mix, keep stirring at 80~95℃ for 1~3h to get pretreated stone;
[0030] (2) Take a citric acid solution with a mass fraction of 20% and add reagent B to mix according to the mass ratio of 3:5~8, add p-toluenesulfonic acid with a mass fraction of 2~5% of the citric acid solution, heat up to 120~160°C, and cool naturally To 70~80°C, distill under reduced pressure to obtain a reduced-pressure distillate, take the reduced-pressu...
Embodiment 1
[0034] Reagent A: Mix oleic acid, glacial acetic acid and water at a mass ratio of 1:4:20 to obtain Reagent A.
[0035] Reagent B: Mix n-octanol and dibenzylidene sorbitol at a mass ratio of 2:1 to obtain Reagent B.
[0036] Silicon-containing material: at 45°C, mix allyl polyether, hydrogen-containing polysiloxane, and sodium allyl sulfonate in a reaction kettle at a mass ratio of 3:2:1, stir magnetically at 400r / min for 40min, add Mix the catalyst with 1% mass of allyl polyether, raise the temperature to 80°C, and keep it warm for 3 hours to obtain the silicon-containing material.
[0037] Catalyst: Mix chloroplatinic acid and isopropanol at a mass ratio of 1:30 to obtain a catalyst.
[0038] Auxiliary materials: Mix talcum powder and diatomaceous earth at a mass ratio of 3:2 to obtain auxiliary materials.
[0039] Surfactant: Mix fatty alcohol polyoxyethylene ether and alkylphenol polyoxyethylene ether at a mass ratio of 3:1 to obtain a surfactant.
[0040] Additive: Mix...
Embodiment 2
[0047] Reagent A: Mix oleic acid, glacial acetic acid and water at a mass ratio of 1:8:20 to obtain Reagent A.
[0048] Reagent B: Mix n-octanol and dibenzylidene sorbitol at a mass ratio of 5:1 to obtain Reagent B.
[0049] Silicon-containing material: at 65°C, mix allyl polyether, hydrogen-containing polysiloxane, and sodium allyl sulfonate in a reaction kettle at a mass ratio of 7:2:1, stir magnetically at 700r / min for 60min, add Mix the catalyst with 4% mass of allyl polyether, raise the temperature to 95°C, and keep it warm for 5 hours to obtain the silicon-containing material.
[0050] Catalyst: Mix chloroplatinic acid and isopropanol at a mass ratio of 1:50 to obtain a catalyst.
[0051] Auxiliary materials: Mix talcum powder and diatomaceous earth according to the mass ratio of 6:2 to obtain auxiliary materials.
[0052] Surfactant: Mix fatty alcohol polyoxyethylene ether and alkylphenol polyoxyethylene ether at a mass ratio of 7:1 to obtain a surfactant.
[0053] A...
PUM
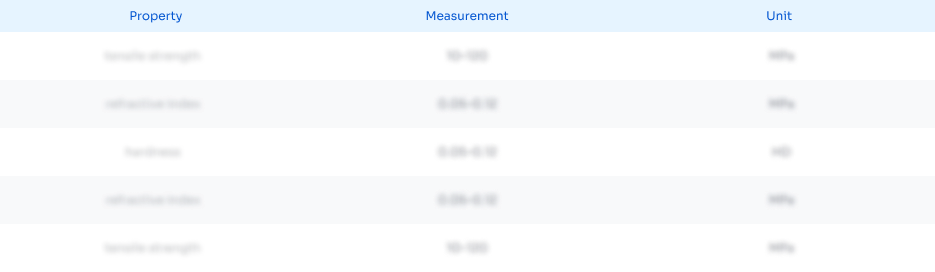
Abstract
Description
Claims
Application Information

- R&D
- Intellectual Property
- Life Sciences
- Materials
- Tech Scout
- Unparalleled Data Quality
- Higher Quality Content
- 60% Fewer Hallucinations
Browse by: Latest US Patents, China's latest patents, Technical Efficacy Thesaurus, Application Domain, Technology Topic, Popular Technical Reports.
© 2025 PatSnap. All rights reserved.Legal|Privacy policy|Modern Slavery Act Transparency Statement|Sitemap|About US| Contact US: help@patsnap.com