Processing method for large-thickness composite skirt
A processing method and composite material technology, which are applied in the field of resin-based fiber reinforced composite material prepreg autoclave molding, can solve problems such as poor quality stability, and achieve the goal of improving quality, compacting tightness, and improving interlayer bonding quality. Effect
- Summary
- Abstract
- Description
- Claims
- Application Information
AI Technical Summary
Problems solved by technology
Method used
Image
Examples
Embodiment 1
[0028] see Figure 1-7 . The embodiment of the present invention provides a method for processing a large-thickness composite material skirt 1 . The processing method of this composite material skirt 1 comprises the following steps:
[0029] S1. Prepare materials: thaw the composite material sheet, and cut the composite material sheet.
[0030] S2. Preparation of the mold 2: cleaning the mold 2, and applying a release agent on the mold 2. After the processing is completed, the demoulding process can be conveniently carried out.
[0031] S3. Laying: the steps of laying include:
[0032] S31. Design a lay-up scheme;
[0033] S32. Laying the composite material on the mold 2 according to the laying plan.
[0034] specific:
[0035] S31. Design the lay-up plan: first establish the three-dimensional model of the composite material skirt 1 through three-dimensional modeling software, then analyze the structural characteristics and load conditions of the composite material skir...
Embodiment 2
[0050] The embodiment of the present invention provides a processing method for a large-thickness composite skirt 1, which is basically the same as the processing method provided in Embodiment 1, the difference is that in the embodiment of the present invention, in the laying process , the composite skirt 1 is pre-compacted by hot-pressing pre-compacting method.
[0051] Specifically, the processing method of the composite skirt 1 provided in the embodiment of the present invention includes:
[0052] S1. Prepare materials: thaw the composite material sheet, and cut the composite material sheet.
[0053] S2. Preparation of the mold 2: cleaning the mold 2, and applying a release agent on the mold 2. After the processing is completed, the demoulding process can be conveniently carried out.
[0054] S3. Laying: the steps of laying include:
[0055] S31. Design a lay-up scheme;
[0056] S32. Laying the composite material on the mold 2 according to the laying plan.
[0057] In ...
Embodiment 3
[0065] This embodiment provides a processing method for a large-thickness composite skirt 1, which is basically the same as the processing method provided in Embodiment 1, the difference being that in the embodiment of the present invention, during the lay-up process, The pre-compaction of the composite skirt 1 is carried out by two methods of normal temperature pre-compaction and hot-press pre-compaction.
[0066] Specifically, the processing method of the composite skirt 1 provided in the embodiment of the present invention includes:
[0067] S1. Prepare materials: thaw the composite material sheet, and cut the composite material sheet.
[0068] S2. Preparation of the mold 2: cleaning the mold 2, and applying a release agent on the mold 2. After the processing is completed, the demoulding process can be conveniently carried out.
[0069] S3. Laying: the steps of laying include:
[0070] S31. Design a lay-up scheme;
[0071] S32. Laying the composite material on the mold ...
PUM
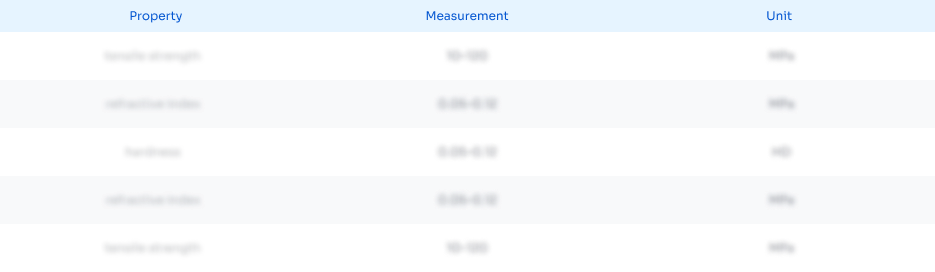
Abstract
Description
Claims
Application Information

- R&D
- Intellectual Property
- Life Sciences
- Materials
- Tech Scout
- Unparalleled Data Quality
- Higher Quality Content
- 60% Fewer Hallucinations
Browse by: Latest US Patents, China's latest patents, Technical Efficacy Thesaurus, Application Domain, Technology Topic, Popular Technical Reports.
© 2025 PatSnap. All rights reserved.Legal|Privacy policy|Modern Slavery Act Transparency Statement|Sitemap|About US| Contact US: help@patsnap.com